Low stress and good flow are what all producers want when putting cattle through a handling system.
Oftentimes though, cattle balk at something or just don’t flow as smoothly as they should.
That’s the situation Craig Lehr found himself in, even though he had a “very well-built” one-piece, S-alley livestock-handling system with a crowding tub that, in its day, was considered a very good system.
“However, the cattle just didn’t like it,” said the third-generation Medicine Hat-area rancher.
“When you saw the cattle, you knew we were being hard on them.”
Read Also
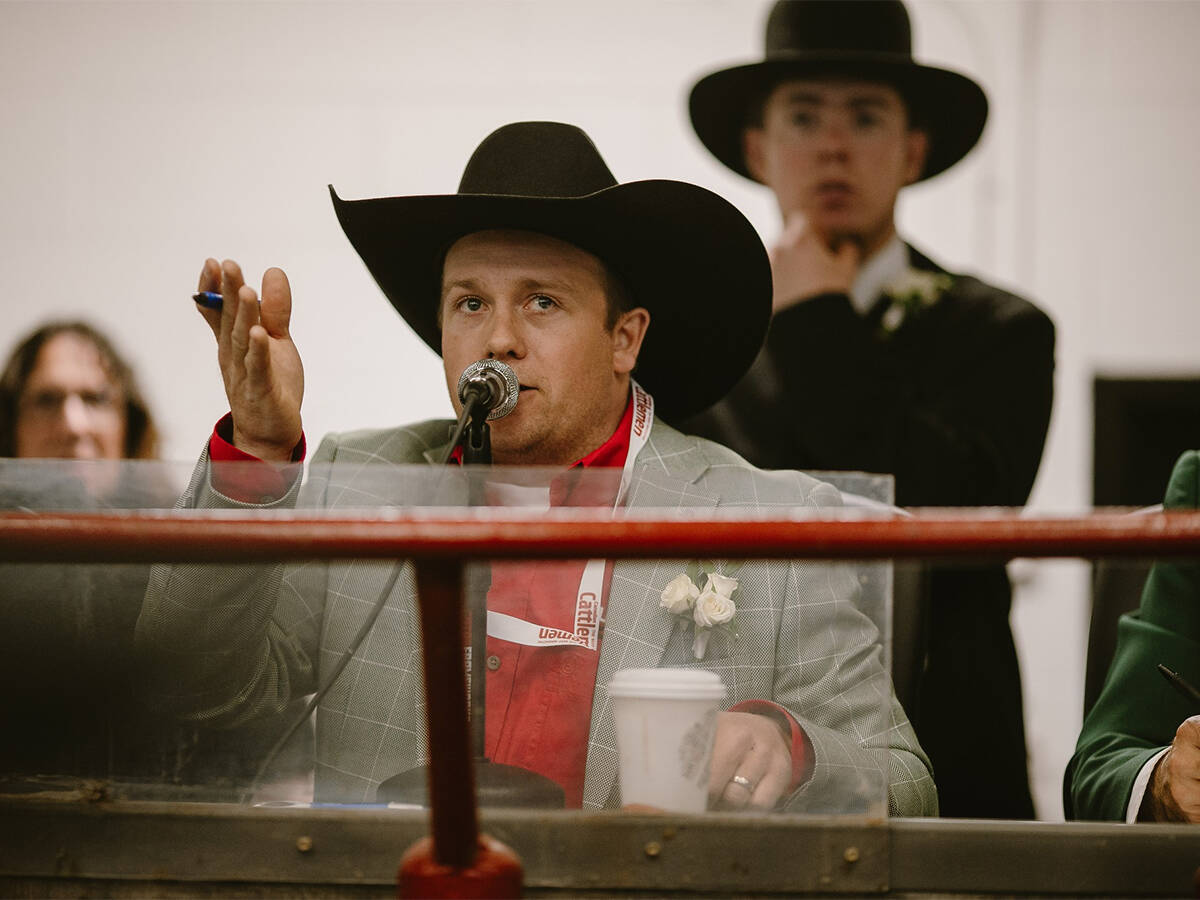
Auctioneering runs in Lawes family’s blood
A genuine personality and respect for ranchers helped Casey Lawes of Provost, Alberta win the Livestock Markets Association of Canada’s auctioneering championship.
It not only required a lot of yelling and prod use to get the cattle to move through the system, he noticed that once they had been through once or twice, they didn’t want to go back through again.
“We looked at updating that system and trying to make some improvements to get some better cattle flow,” said Lehr, who with his family, owns and operates Short Grass Ranches, which backgrounds 7,000 head throughout the year and has a 1,200-head cow-calf operation.
“As we got into things a little further, we decided to upgrade the entire system.”
Lehr sorts a lot of cattle in the feedlot. They’re placed in pens upon arrival. As the cattle grow and they develop a marketing plan, from February to August, Lehr starts size sorting.
“We’re always continuously sorting cattle, getting groups ready to sell.”
So a better way to sort topped the priority list when he started looking at upgrading his system.
“We sort all these cattle in a 16-feet-wide by 80-feet-long alley, and it involved gates getting smashed, people getting hurt, hit by cattle. It was a dangerous thing to do,” he said. “With more employees around all the time, people were getting hurt, and inexperienced people were getting put in positions they shouldn’t be in.
“I was trying to find a better way to sort cattle.”
His research and visits to other feedlots led him to Daniels Manufacturing Co., which uses open sides in its handling system. Lehr liked that as he sorts feedlot cattle not just by weight but also by body type.
“This way we can still visually see the animals.”
Since Lehr is sorting cattle often, he added a hydraulic sort system at the front end of the handling system.
“Now we just feed cattle through the system,” he said. “The person sorting can visually sort and run all the gates off hydraulics. Now, we can sort 300 to 400 head an hour and sort three to four different ways.
“There isn’t one raised voice, there isn’t one person getting hit, no gate smashing, nothing. That was the main aspect I was looking at changing.”
The new system
When the switch from old to new was made in 2016, Lehr changed the direction of the system. The old system faced to the south, which meant cattle were always going towards the sun, a problem exacerbated in wintertime. The new system faces north, and while there are shadows at parts of the day, cattle aren’t forced into bright light.
As well, the crowding tub was swapped out for a Bud Box, allowing the animals to flow more freely into a double-entry alley that narrows down (via a gate the cattle manoeuvre themselves) to a single alley where body condition and type are evaluated. The alley itself is hydraulic adjustable, too, as are the backstops, so calves can’t turn around in the alley.
The cattle exit the alley through the hydraulic chute before they enter the sort system. Lehr purchased a five-way sort system, but can only sort four ways so he fed the hydraulics into the remote and onto the back door of the squeeze. So now the person running the hydraulics can start and stop cattle before they get into the sort system by using the tailgate on the chute. The cattle have no issues going through the chute to exit the alley when they are sorting because they are able to open it wide enough.
Lehr has found many benefits of his new system, the biggest being the calmness of the cattle.
“Their behaviour is so different after compared to the old system,” he said. “They come out of the system, they go into the holding areas, and they just stand there.
“They are calm, they aren’t worked up. It’s really nice to see the change in the cattle.”
The system works well for the handlers, too.
“For me personally, and the employees, we can stand there and process cattle all day. Nobody is miserable and grumpy at the end of the day,” said Lehr.
“With the old system, there was people yelling, things weren’t going well, and nothing went smoothly; the sooner you could get it done, the better. Now it’s a relaxed, calm, quiet atmosphere; nobody minds being there.”
The new system has also reduced the labour component.
“Many jobs — like branding and implanting — require one less person and yet we are still able to process the same or even more head per hour than before.”
However, there’s more staff training now.
“It doesn’t matter what you have for a system, if the cattle aren’t being handled properly then you lose all the advantages of a low-stress system. Productivity goes down and stress goes up,” Lehr said. “It takes some stockmanship skills and training to move cattle through a system in a calm, yet efficient, low-stress manner to get the job done.”
It’s also gratifying to see light bulbs go on — when employees realize that doing the right thing is also easier.
Lehr was able to obtain Growing Forward funds, covering about half the costs. Making the changes to accommodate the new system also required adding some extra pens. The entire project was approximately $80,000.
But you don’t have to spend a lot of money to get better results from your system, he said.
“If you watch your cattle and learn about how they move, there is a lot of things with systems that can be changed.”
That can be as simple as changing the location of a gate or the way cattle come up and enter the handling system.
“Those things don’t cost a lot. It doesn’t have to be huge changes, it’s small things you can change that make a huge difference in the flow of cattle.”