Alberta farmers grow lots of pulses and most Albertans eat beans, peas, lentils or chickpeas at least occasionally, but stores in Alberta have not been able to offer shoppers Alberta-grown product.
Joerg and Petra Klempnauer aim to change that.
As a farmer, Klempnauer grew a variety of pulses at Grassy Lake, near Bow Island. He then bought Columbia Seed Limited, a seed company supplying pulse growers in Canada and overseas with vining pea seed for fresh markets and marrowfat pea seed.
Klempnauer expanded into other pulses, brokering Alberta lentils, yellow and green peas, marrowfat peas, chickpeas, beans, and fababeans to buyers around the world. He also upgraded seed processing to offer treated and inoculated seed with a polymer coating.
Read Also
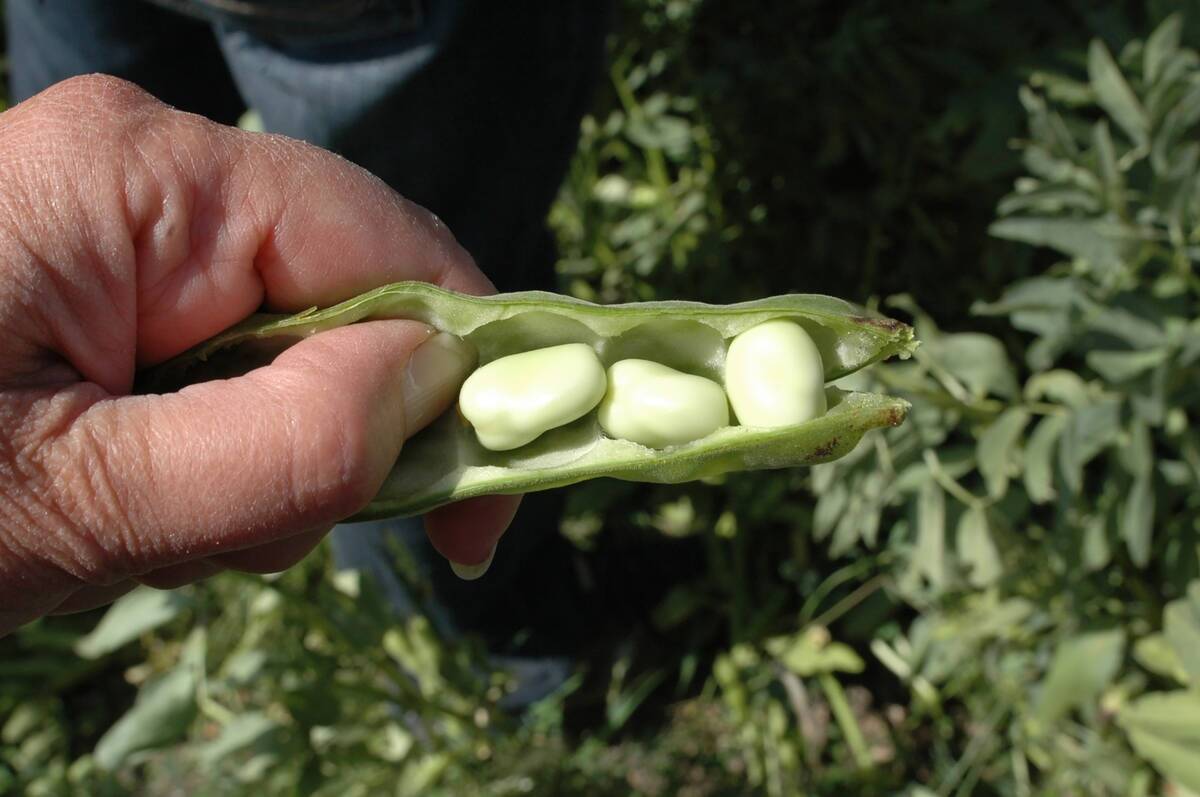
New crop insurer policy enables easier startup for faba beans
Agriculture Financial Services Corporation updated its normals for faba beans, which may open the door for more Canadian producers to feel comfortable growing the pulse crop in the future.
A reputation for quality boosted sales and demand soon exceeded the capacity of his original small elevator.
“We have to be flexible and ready to process any pulse crop,” says Joerg. “We started to upgrade, expanding, and putting in new equipment in 2008. We’ve sold the farm, bought land at Vauxhall (north of Taber) for a plant and we’re building a house here.”
The new plant can provide the quality demanded by most Columbia Seed customers clean, shiny seeds that appeal to relatively affluent consumers, and the retailers who sell to them. The new plant will allow the Klempnauers to create a new line of pulse products aimed at the domestic market.
The facility is designed for processing and packing all sorts of pulses. The crew is particularly happy with the palletizer that automatically stacks bags ready for shipping.
“It’s a huge relief for the workers – not having to load pallets with 50 kg bags,” says Joerg. “We can auto-load a container in 20 minutes and run the plant with three, instead of seven, workers. We’ve also increased the capacity of the cleaning line – we can run at 10 to 40 tonnes an hour, depending on the market we’re selling into.”
The new plant includes a 60-by 120-foot warehouse with office space on a second floor. There’s also bulk storage for clean crop with four bins that each hold a container load of ready-to-ship product. Cleaners, optical colourchecking machines, polishers and bagging systems are at one end of the warehouse. At the other end is a system for processing pulses for the domestic market.
That’s an exciting new development that will eventually lead to 20 products in packages sized for grocery stores and labelled as produce of Alberta.
Developing products for the domestic market is complex and the Klempnauers are proceeding one step at a time. They’ve developed a HACCP (hazard and analysis critical control point) plan for food safety and gone through the daunting process of winning CFIA approval for the plan.
The Klempnauers have developed a snack food call Crispeas that Petra has been selling direct to consumers and through farmers’ markets. They are made from marrowfat peas, are high in protein and fibre, and can also be used as a salad topping. Crispeas are very popular among people who’ve tried them and some large companies have approached Klempnauers for the rights to distribute them. This spurred the development of the HACCP-approved plant and process, a regulatory requirement for selling processed food through retailers.
Marrowfat peas are a new crop for many farmers.
“They take a little more dedication and better ground than dry peas,” says Klempnauer. “The main thing is you have to combine them when they’re ready, not 10 days or two weeks later. But, there are returns for quality – $12 (a bushel) compared to $6 for green peas.”
The couple, who both work full-time in the business along with their eldest son, source most of their pulses from within a 100-kilo-metres radius of their Vauxhall plant , some grown under irrigation and some on dryland.
———
“We have to be flexible and ready to process any pulse crop.”
JOERG KLEMPNAUER