Watch for a full version of this story in the August-September issue of Country Guide East.
Is storage and drying part of doing business in this modern era of farming? Or is it a type of on-farm management that growers should leave to the professionals?
It all depends on who’s answering those questions.
Across much of Eastern Canada, more growers are building, replacing or expanding storage and drying units. It’s much like the decision between owning equipment versus hiring custom operators. The former provides more immediacy and convenience — you have the machinery when you need it, but at a greater cost. The latter offers less initial cost but greater risk of delayed planting, spraying or harvesting.
Read Also
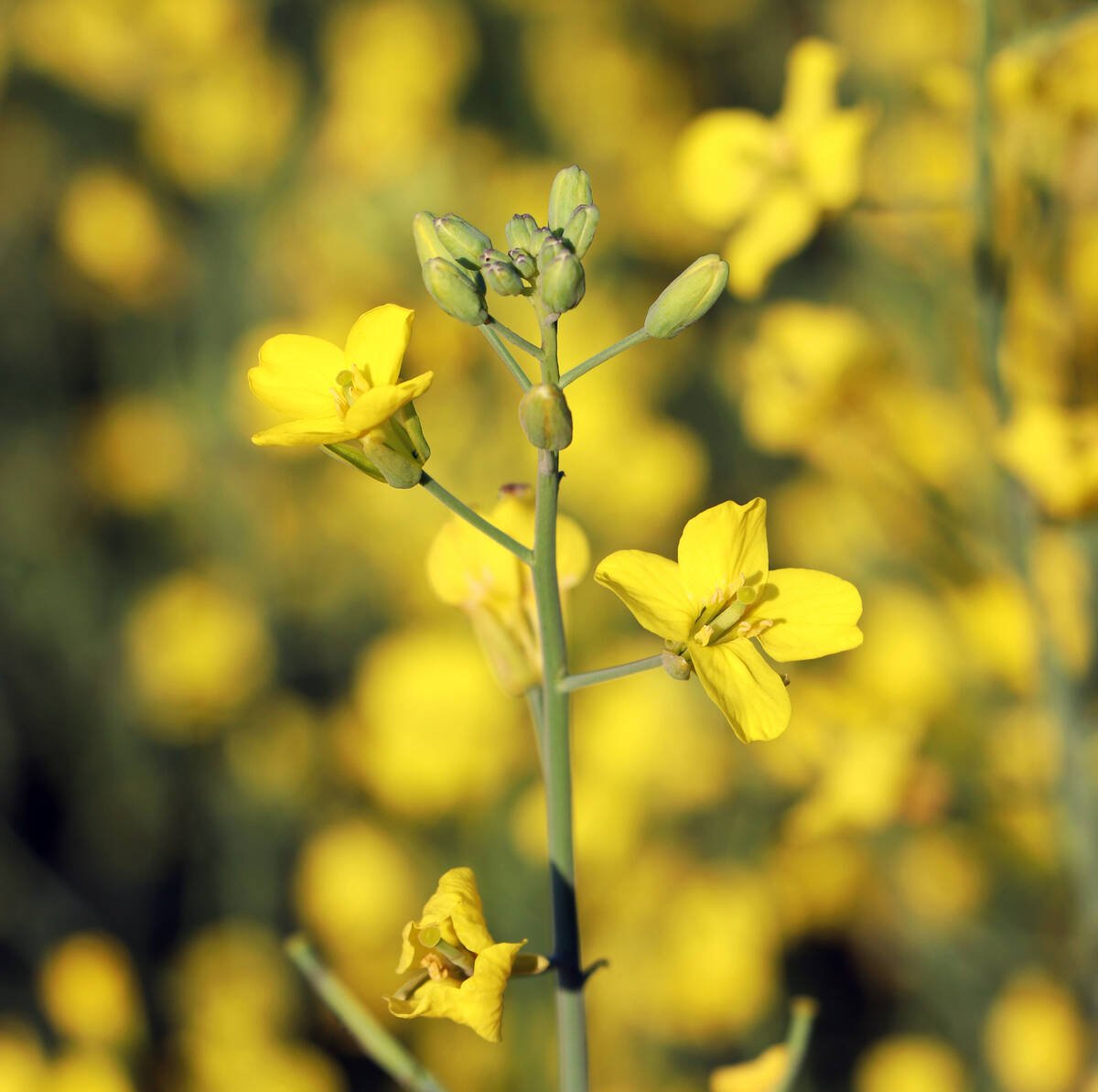
ICE Weekly: Soyoil influencing canola prices
Chicago soyoil prices seem to be the main influencer of canola’s price movement during the week ended Aug. 27, 2025.
Some farmers want that immediacy and convenience, and look at it as a cost of doing business and a matter of improving on-farm logistics and marketing. Unless you are next door to an elevator and can unload easily without significant wait times, then the move towards larger farms and more and more widespread fields necessitates on-farm storage and drying systems.
However not all new storage and drying units are a simple case of easing logistics and enabling better marketing plans. Helmut Spieser, engineer with the Ontario Ministry of Agriculture, Food and Rural Affairs (OMAFRA), agrees that larger farms with higher yields need more storage. Some growers are even constructing new units in the hopes of becoming, in effect, inland grain terminals for some of the larger elevators. But it’s not as simple as it all may seem.
"If they have the assumption that ‘just because I put a system, I’m going to make a whack of money,’ they’re going to be disappointed," cautions Spieser. "There’s opportunity there with contracting and getting paid to keep it for six months or whatever the time may be, as an incentive, so that the mill doesn’t have to store it. You store it on farm and they’ll pay you for doing that, but then with you conditioning and storing your own grain, you are now the keeper of the quality."
In effect, there is too much at stake to take anything for granted. Wheat’s current pricing structure, its sprouting potential and its specific quality uses within the food industry, all add to the stakes. That’s why Spieser shares an observation he heard from another person: if you have a large on-farm system, you should have one person dedicated to its management. It shouldn’t be left to someone in a part-time capacity or considered something that fills in the time between chores.
Insect pests are another threat. Since wheat is harvested at the height of summer, it’s also the height of insect activity, and as Spieser notes, it’s the first "fresh food" in the bin.
Speiser says it’s one thing to say "This farmer says he pays 19 cents shipping whereas the mill is charging 51 cents," but he contends that these comparisons are not "apples to apples." The price the farmer may be quoting could be for fuel, alone. The price the mill quotes usually includes everything: overhead, insurance, profit, amortization, repairs, demurrage and equipment breakdown.