Though there are still a few bugs to work out, the speed of NIRS technology and its potential for cost saving has made it a hit with feedlots
Grants for rapid-feed analysis machines are still available for Alberta livestock producers and feeders, but they’ll have to apply soon.
Thanks to $750,000 in funding from the Alberta Livestock and Meat Agency producers can buy Near Infrared Reflectance Spectrometry (NIRS) equipment for their farms at a reduced cost. So far, 28 applications have been approved, which leaves enough funding for eight to 10 more machines.
“The NIRS equipment grant provides some cash dollars up to 50 per cent for people to buy NIRS equipment,” said Rob Hand of Alberta Crop Industry Development Fund, which is administering grants.
Read Also
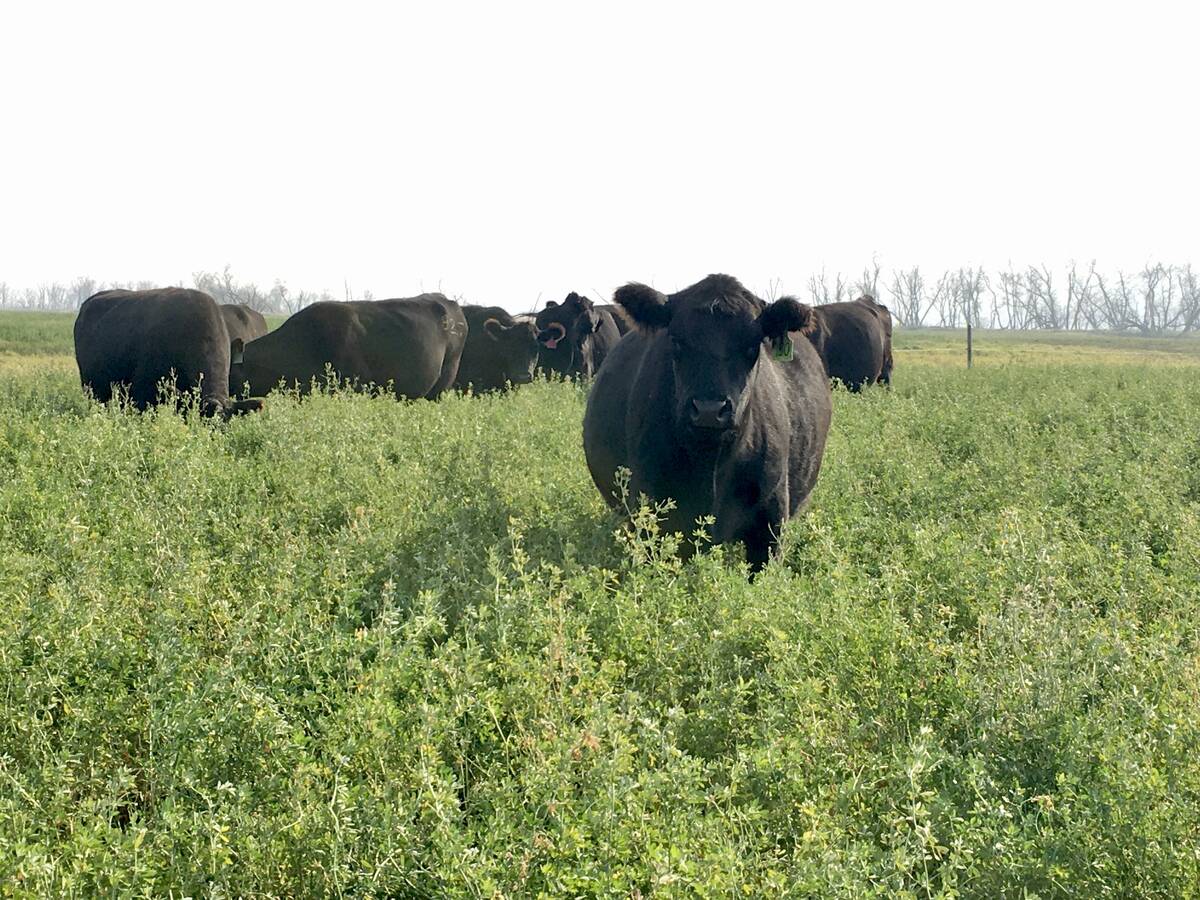
ABP opens up about leaving CCA
Alberta Beef Producers is leaving the Canadian Cattle Association due to concerns about fiscal transparency and governance, ABP officials say.
“And it’s not all spent. Even though there’s 28 machines out there, there’s still 10 machines that we have funds for.”
The same technology is used in grain terminals to detect moisture and protein, but was too pricey for most livestock operations in the past. But with costs coming down, this type of feed-analysis technology is in reach of those who couldn’t afford it before, said Marylou Swift, research scientist with Alberta Agriculture.
“We now have industries that have purchased the equipment, and they can get an energy digestibility on their grain, as well as starch content, fibre content, protein content, and moisture content,” she said. “Beef feedlots have been a big uptake of this technology.”
The technology is very useful in determining uniformity feed rations. Oil content in distiller grains and energy content in barley grains can vary by as much as 20 per cent, making it hard to know exactly what’s going into the feed.
“It’s better to know what you’re dealing with,” said Swift. “We went to look at one company, and they brought in truckloads of wheat that varied anywhere from 11 to 16 per cent. That has a huge impact on animal performance.”
The real benefit, however, is its speed.
“You take a sample, you run it through, and 30 seconds later, you can tell how much oil, starch, protein, and moisture is in that sample,” she said. “And you can use this to reformulate your rations or make purchasing decisions on suppliers.”
Compared to wet chemistry, NIRS is “instant technology,” but its speed comes at a price.
“You have to actually calibrate it, and it requires some expertise to develop these calibration equations,” said Swift. “You have to have somebody — and that somebody right now is me — who can collect samples and put them all together and develop calibration equations. And then you have to maintain them.”
Right now, making and maintaining calibrations is the “biggest headache” involved with using NIRS technology, says Swift.
“Using them on farm is no challenge at all. It’s just maintaining these calibrations and getting them to where they’re stable. We’ve been at that for a while now, so I think we’re getting pretty close to that situation.”