Because feed cost represents the largest proportion of the overall cost of production, efficient use is key to profitability.
Feed efficiency is influenced by many factors — including diet formulation, availability of amino acids, the feed manufacturing process, pig health, and barn management, Steve Dritz, from Kansas State University, said at the recent Red Deer Swine Technology Workshop.
“Decisions to optimize feed efficiency range from global decisions such as choosing the optimum sire line to management at the barn level that includes environmental and feeder management among others,” he said.
Read Also
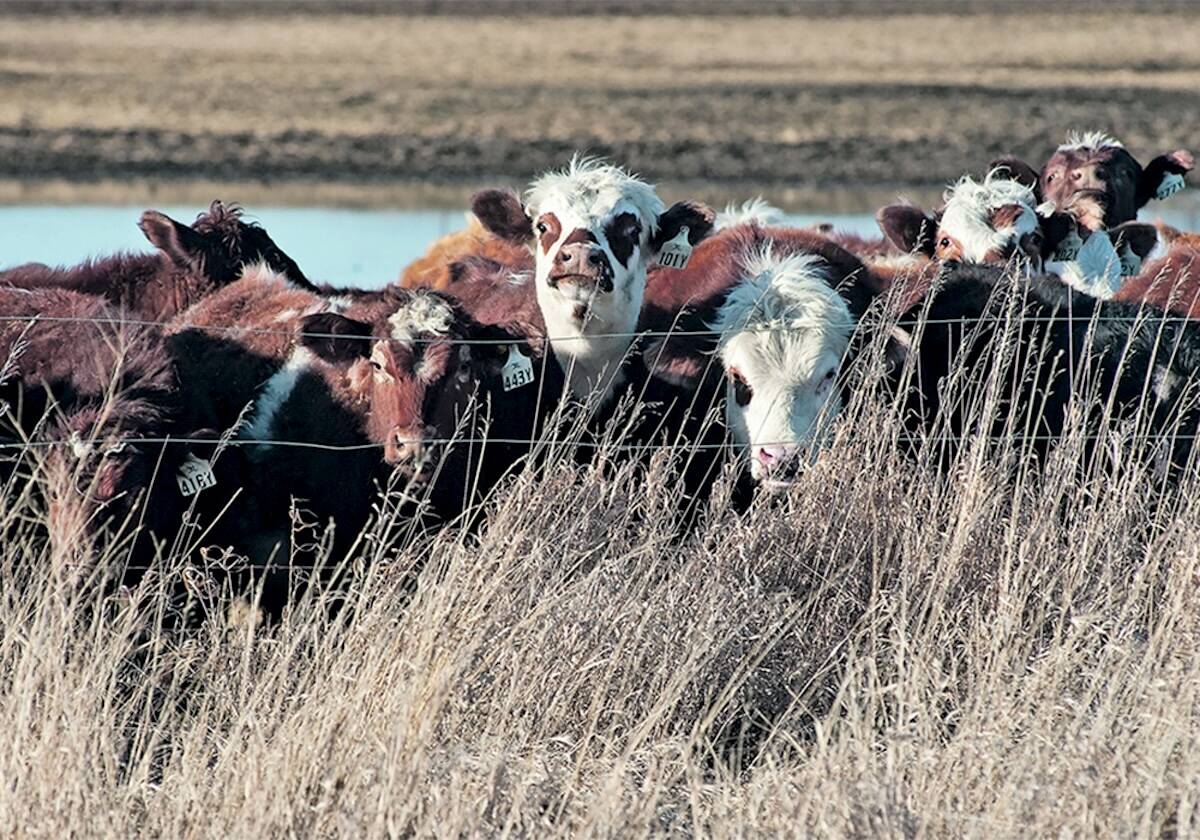
Alberta Beef Producers announces withdrawal from Canadian Cattle Association
Alberta Beef Producers announced its withdrawal from the Canadian Cattle Association, effective July 1, 2026.
Feed efficiency or feed-to-gain ratio is simply the amount of feed used to produce one unit of weight gain, but it is important to ensure comparisons with industry data are made on the same basis, said Dritz. “The accepted way to calculate close-out feed efficiency in a production system is total feed delivered divided by the start weight minus the sale weight,” he said. “However, this doesn’t include dead pig weight. Accounting for dead pig weight will lead to a better feed-to-gain ratio. However, the improvement is not directly linked to a better economic outcome.”
He also noted feed efficiency is dependent on weight range because feed-to-gain ratio worsens as pigs get heavier. This means that when comparing farm data, the start and finish weights should be adjusted to be the same, using a formula, in order to make a fair comparison. “Another area to understand when measuring feed efficiency is the influence of dietary energy density,” said Dritz. “Dietary energy will influence growth rate and feed intake and consequently feed per unit of gain. Therefore, many production systems are calculating feed efficiency as calories per unit of gain.”
Also, since different ingredients influencing dietary energy density will also affect carcass yield, a further refinement is to calculate caloric efficiency per unit of carcass gain, he added.
Proper diet formulation
Various aspects of diet formulation will impact feed efficiency, but one important factor is ensuring an adequate supply of amino acids. “The use of 20 grams of standardized ileal digestible (SID) lysine per kilogram of gain appears to be a reasonable estimate of the lysine requirement of finishing pigs,” Dritz said. “Thus, once a growth curve and feed-intake curve are obtained from pigs within a production system, the lysine requirement curve can be estimated with reasonable accuracy.
“The next step is to ensure that other essential amino acids are at a minimum ratio relative to lysine. Although the order can vary with different dietary ingredient mixtures, typically the first five limiting amino acids for most practical diets are lysine, threonine, sulphur amino acids, tryptophan, and valine. Due to increasing economical availability of crystalline lysine, threonine, and methionine, tryptophan is commonly the limiting amino acid in practical diet formulation.”
Work at Kansas State suggests that a minimum ratio for tryptophan to lysine of 18.5 per cent is required for finishing pigs. Quality feed manufacturing starts with optimizing grain particle size, Dritz stressed. “A general rule of thumb is that feed efficiency improves 1.2 per cent for each 100-micron decrease in particle size, worth approximately 75 cents to $1 per pig,” he said. “From a practical standpoint, we recommend 500 to 600 microns as measured with a 13-high sieve set without a flow agent for grain fed in meal form. Smaller particle sizes can be used in finishing pigs providing flowability is maintained or when diets are fed in pellet form.”
In addition, he said, when using pelleted diets, smaller particle sizes will improve pellet mill throughput. Another consideration is to ensure adequate mixing of diets, especially with low inclusion products such as synthetic amino acids and phytase. Frequent monitoring of mixers to evaluate coefficient of variation is essential, Dritz said.
Barn management influences efficiency
The stockperson can have a major influence on feed efficiency, he noted.
“After pigs enter the barn, daily chores that influence overall feed efficiency include individual pig treatment and timely euthanasia, ensuring water and feed availability, feeding the appropriate diet, managing the air quality and environmental temperature, properly adjusting feeders and handling pigs in a positive manner,” he said. “Removing a portion of the pigs from all pens during initial marketing can result in feed savings while maximizing weight produced from the facility. Withdrawing feed prior to market also can result in feed savings.”
Dritz emphasized the importance of feeder design in minimizing feed wastage, which can be a drain on feed efficiency.
“On a yearly basis, feeders in the grow-finish barn are each dispensing $12,000 or more of feed,” he said. “When selecting feeders for finishing pigs, we follow four principles: The adjustment mechanism should be easy to use and durable, the width of a single feeding space should be a minimum of 35 centimetres, the depth should be at least 25 centimetres, and there should be trough dividers to give some degree of protection to the pig while feeding.”
The dividers force the pig to stand at right angles to the feeder to eat, resulting in decreased rooting and pig-to-pig interaction.
“Ultimately, optimizing feed efficiency is a multi-faceted process that requires commitment from all levels of production and continuous re-evaluation to ensure that best practices are in place,” Dritz concluded.