Bernie Peet is president of Pork Chain Consulting Ltd. of Lacombe, Alberta, and editor of Western Hog Journal.
With around 80 per cent of the feed required to produce a market hog being used during the growing and finishing stage, any changes in efficiency can have a huge effect on margins. In a video presentation produced by the Red Deer Swine Technology Workshop, Pat Monaghan, production manager with Paragon Pork Management discusses some of the factors that impact margins and demonstrates the key aspects of managing grow-finish systems.
Read Also
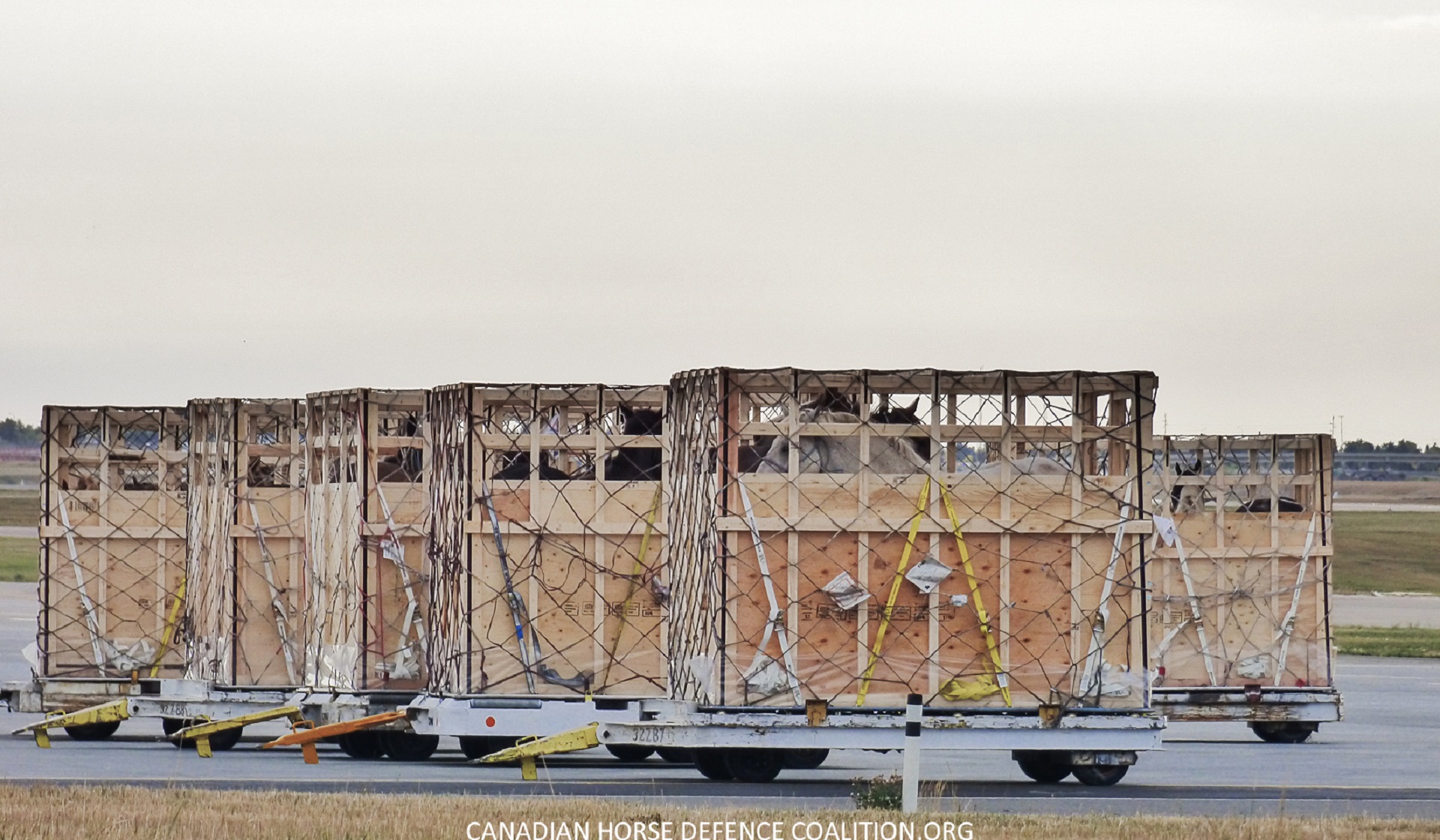
Horns aren’t unlocking anytime soon on livestock transport standards
Standards good enough meet the definition of “humane” animal transportation still vary widely between what what industry wants, what animal rights advocates want and, between the two, what federal regulators decide is good enough.
The video was shot at two finishing barns in central Alberta that take pigs from Eclipse Pork, a 2,500-sow operation near to Lacombe, which has a separate off-site nursery. One barn has conventional pens with 50 pigs per pen, while the other is a large group auto-sort system with 500 pigs per pen.
Rapid growth and efficient use of feed are the most important factors influencing margins, says Monaghan. The starting point is the quality of pigs coming from the nursery, he notes. “Transferring heavier pigs into the finishing barn not only results in faster growth but lower mortality and morbidity, improved feed efficiency and better carcass quality,” he stresses. “Our average weight at entry is 27 kg, which means that pigs get off to a flying start.” Research suggests that a one-kilo heavier pig results in 2.5 – 3.0 kg higher carcass weight or three fewer days to market weight.
Pig health has a major effect on performance, so it is important that a health plan is developed by the veterinarian, which includes routine vaccinations and treatments. “We carry out vaccinations for circovirus and ileitis in the nursery, which means that the need for treatments in the finisher barn is minimized,” Monaghan explains. “Also, each barn has a detailed treatment protocol which shows exactly how to deal with the health problems most likely to be experienced in individual pigs.” The protocol also helps to control veterinary costs, he adds.
In order to minimize the impact of health problems on pig growth, detailed daily health checks and rapid treatment of sick, injured or disadvantaged pigs are essential. This is a lot more difficult in a large group system, Monaghan notes. “Although it sounds simple to carry out a health check, with such a large number of animals it is easy to miss pigs that need attention,” he says. “It is essential not only to spend enough time walking the pens but also to ensure that all pigs are carefully observed, which requires diligence and a good knowledge of pig behaviour.”
FEED INTAKE KEY TO RAPID GROWTH
Maximizing feed intake is the key to achieving rapid growth up to market weight, Monaghan believes. “We pay a lot of attention to the factors that influence intake and we monitor it for each batch of pigs through the system,” he says. “We have seen average feed intake vary between 2.15 and 2.5 kg/day. Low feed intake could be due to incorrect feeder adjustment so that feed availability is reduced, while a very high feed intake could be the result of wastage.”
Monaghan details the most important factors to consider as:
Ensuring there are enough feeders for the number of pigs in the pen.
Providing the correct space allowance per pig – inadequate space reduces feed intake, irrespective of the number of feeders.
Adjusting feeders to provide easy availability of feed without resulting in wastage.
Carrying out daily checks for correct drinker operation.
Where possible adjusting drinker height to be at shoulder height of the smallest pig in the pen.
Reducing environmental temperature steadily as pigs grow in order to stimulate appetite. Within the Eclipse finishing barns, temperature at entry is 21.5C, which is gradually reduced to 16C by the time the pigs reach 90-kg live weight.
FEEDERS AFFECT EFFICIENCY
Because feed represents by far the largest cost during the finishing stage, it’s important to maximize the efficiency with which it is converted into pig growth, Monaghan emphasizes. The type of feeder used can have a big effect, he believes. “Most of the Eclipse finishing barns use wet/dry feeders, which lead to a high feed intake without wastage. Of course, correct feeder adjustment is essential to achieve this,” he points out. “Feed quality, especially particle size, also has an impact on the efficiency of feed utilization, so we monitor that very closely.”
Correct feed formulation for pigs at different stages of production, with a different feeding program for barrows and gilts, is essential to minimize feed costs, Monaghan stresses.
Feed budgeting involves feeding a series of diets, which reduce in lysine content as pigs get older and are different for barrows and gilts. This helps to reduce feed costs because overfeeding lysine is very expensive and barrows and gilts have very different requirements for protein relative to their weight. “Five different diets are used within the Eclipse system, the final one including Paylean,” Monaghan says. “While the same diets are fed to barrows and gilts, the timing of diet changeovers differ and the fourth diet is fed to barrows only.”
The other side of the margin equation is the value realized for the market hog and the main influence on this is the percentage of hogs in the processor’s “core” weight range, Monaghan notes. “A good target for this is 90 per cent or more in the core, which requires accurate selection of market hogs,” he says. “In the barns with auto-sort, automatic weighing makes this a lot easier, but it’s crucial to train pigs to go through the scale soon after they enter the barn.”
Copies of the half-hour video, in DVD format, are available from Pork Chain Consulting Ltd., Phone: (403) 782-3776, Fax: (403) 782-4161. They cost $40 each, including shipping, and cheques should be made payable to Swine Technology Workshop.