Research into optimizing barn design and reducing barn emissions among the highlights of the centre’s 2012 research report
The Prairie Swine Centre, which recently celebrated its 20th anniversary, is a resource that benefits pork producers across Canada by carrying out near-market research and providing technical information.
In addition to its research, it maintains a comprehensive database of technical references on its web-based Pork Insight, in addition to being the lead communicator for Swine Innovation Porc, a $9.6-million multi-centre initiative aimed at enhancing the competitiveness and differentiation of Canada’s pork industry. The centre’s 2012 research report provides the results of its work in the areas of engineering, nutrition and ethology (animal behaviour).
Read Also
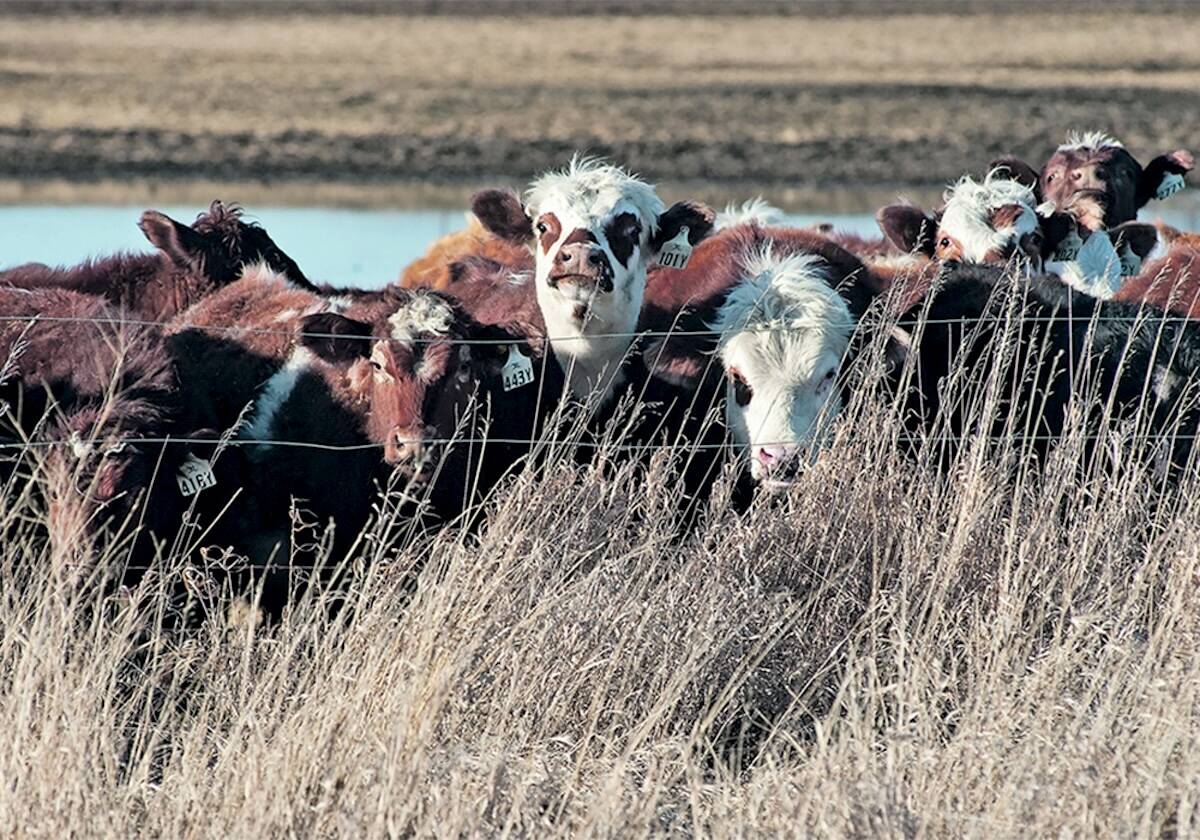
Alberta Beef Producers announces withdrawal from Canadian Cattle Association
Alberta Beef Producers announced its withdrawal from the Canadian Cattle Association, effective July 1, 2026.
Optimizing barn design
Engineers Bernardo Predicala and Alvin Alvarado have been evaluating the current performance of various swine production systems to determine whether standardization and optimization can improve efficiencies and overall productivity. The researchers note that the lack of specific standards for swine buildings often results in increased costs and management inefficiencies. A survey of pork producers found that there was a heavy reliance on “rule of thumb” in making decisions on design, construction and operation of hog barns. The survey identified 14 key problem areas related to equipment such as stalls and crates, pen space, movement and load-out facilities, manure handling, feeders, drinkers and commissioning of equipment.
A second producer survey across Canada revealed that only 18 per cent of producers identified an absence of problems in all of the 14 key areas. Among those who reported encountering issues, the areas most frequently cited were feeders and drinkers (40.9 per cent), space requirements and crowding (39.4 per cent), load-out (34.8 per cent), and farrowing crates (31.8 per cent).
“The specific problems reported include overcrowding, caused by increased prolificacy of breeding herd surpassing the original barn design specifications, and changing market conditions resulting in higher market weights of finished animals,” said Predicala.
“Other common problems with the physical system reported by producers include over 90 per cent of complaints on barn load-out designs, implicating ramp angle and width as the primary problem, as well as 15 to 17 per cent of all respondents identifying flooring type and slatted floor designs as problem areas associated with sow lameness and longevity.”
This work clearly identifies the need for well-defined standards for swine buildings in order to avoid poor design or construction leading to inefficiency, loss of performance and increased costs. It will also help to prioritize future research aimed at improving the areas identified in this project.
Reducing emissions from hog barns
Hog barns emit a number of contaminants into the surrounding air, notably ammonia, hydrogen sulphide and dust. Depending on barn location, this may lead to complaints about smell. The Prairie Swine Centre has previously investigated the use of air-cleaning technology based on “biotrickling filtration,” which involves the use of micro-organisms on a filter medium that break down the contaminants. The system contains packing material, such as wood, ceramics or plastics, and is operated by recirculation of liquid through the packing. A biofilm, the layer of bacteria, is developed on the surface of the packing shortly after the startup of the system. Maintenance of the system involves replacement of the circulating water when the level of contaminants reaches a certain level.
Predicala and Alvarado scaled up the previous experimental units into a commercial-size air treatment unit (ATU), which was then fitted to three grow-finish rooms. The exhaust air from each room was ducted to the ATU and passed through the biotrickling filter.
“The results showed that the air treatment units were effective in reducing the levels of ammonia, dust, and odour from the airstream at the exhaust of the grow-finish rooms by about 77 per cent, 92 per cent, and 75 per cent, respectively,” said Predicala.
“Over the 12-week trial period, levels of ammonia inside the room ranged from 5.2 ppm to 69.1 ppm, while the levels after the treatment units ranged from 4.0 ppm to 11.0 ppm.”
The effectiveness of the ATU in reducing ammonia levels increased over time, from a 22 per cent reduction in the first week to 77 per cent in week 12.
“This implies that the air filtration units worked effectively even at the start of the trial,” Dr. Predicala said. “However, the reduction in ammonia levels during the initial part of the trial was not that high because the ammonia levels in the room were relatively low compared to when pigs were nearly market weight.”
Dust levels post-treatment remained very similar throughout the trial, despite the dust levels in the rooms increasing as pigs grew in size. The maximum dust reduction of 92 per cent was reached in week 12, while the lowest, at 65 per cent, was measured in week three.
The air treatment units consumed an average of 537 litres of water per day, with one unit consuming 663 litres per day. Wide variations in water consumption between ATUs were explained by differences in their efficiency in removing ammonia — the more contaminants that are removed, the more water is required.
“Periodically draining the contaminated water and then adding fresh water into the ATU was necessary to prevent the water from getting saturated, which consequently can adversely impact the biofilm activity on the biotrickling filter media, thereby reducing the contaminant removal efficiency of the system,” said Predicala.
The 2012 Annual Research Report can be downloaded at www.prairieswine.com.