Glacier FarmMedia – Canola growers may one day be able to add food packaging to their list of markets.
New research at the University of Manitoba draws on canola meal protein as a feedstock for biodegradable food product packaging.
“I think it’s a more sustainable solution to the challenges created by all the petroleum-based plastic food packaging materials,” said Thilini Dissanayake, the PhD student whose master’s thesis inspired the project.
Read Also
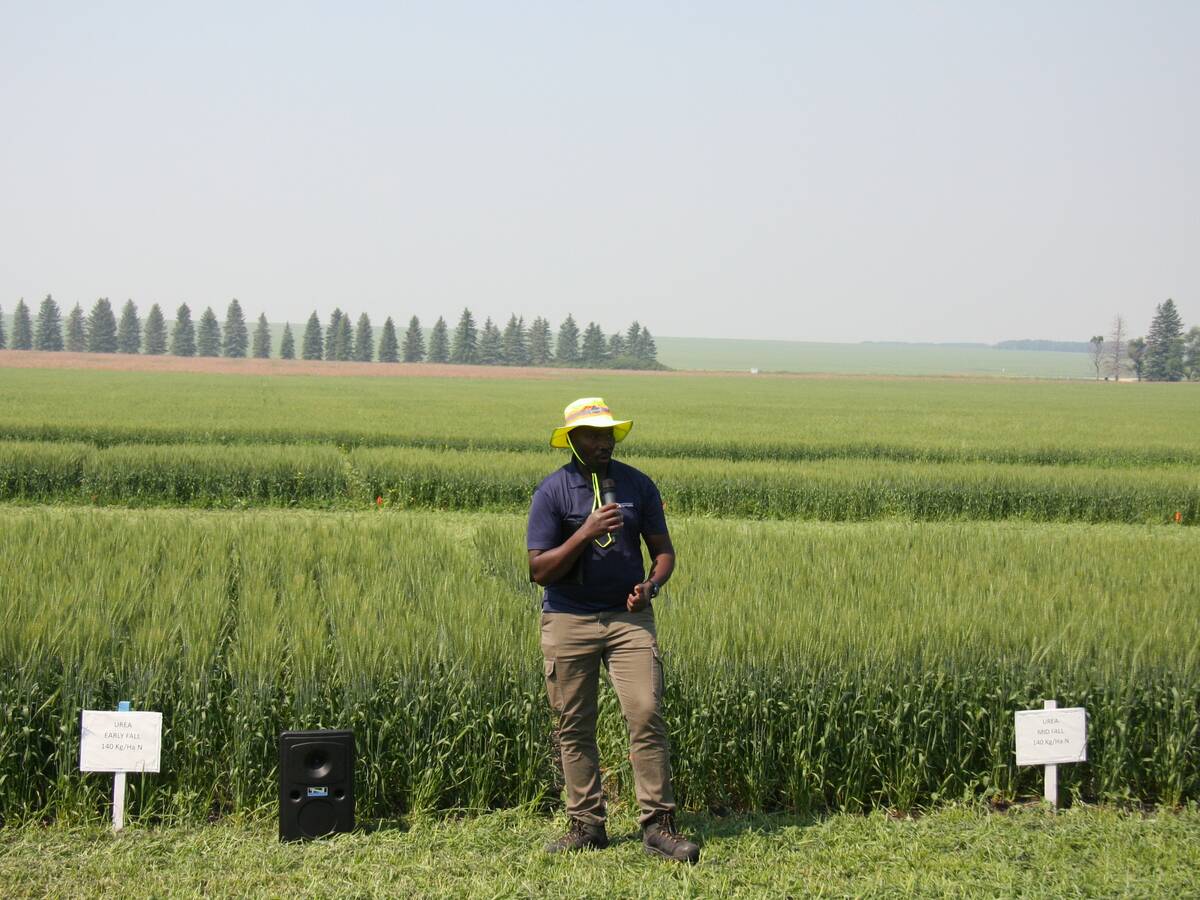
Soil moisture and fall fertilizer loss
A federal research project is working to identify ways to minimize the loss from fall fertilizer applications.
Bans on single-use plastics have fostered a race to find sustainable alternatives, and this one could add value to canola meal.
Many might chuckle at the irony as they fill their reusable grocery bags with item after item wrapped in plastic, but Dissanayake saw it differently. She saw a problem to solve.
“When we think about the future of food packaging materials, we have to think about the environment and the economy,” she said. “The food industry faces a significant challenge in terms of producing packaging materials that are both cost-effective and environmentally sustainable.”
The project looked to one of the most popular crops grown in Western Canada: canola.
More particularly, it looked to the protein from canola meal, which would have the extra benefit of reducing waste on the grain processing end by creating a new market for canola byproducts.
Canola meal is a mainstay for livestock feed, but industry, researchers and organizations like the national Protein Industry Supercluster want to see it move into the human food space.
Food packaging would be a new frontier for canola.
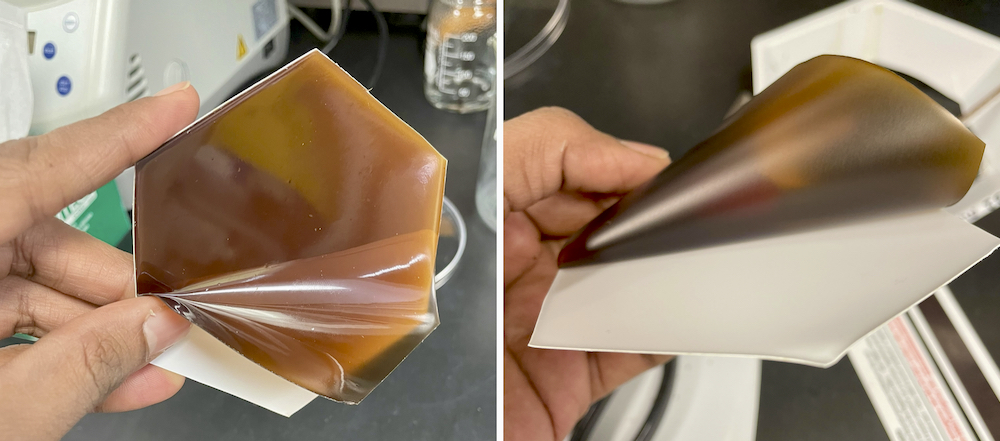
The process
Canola crushers take care of the first step by removing oil from the seed. The canola meal byproduct is then further processed to extract the protein.
The next step is where the magic occurs. The team at the University of Manitoba uses a process called solvent casing to turn that protein into plastic-like film.
Researchers make a solution that includes the canola protein, water and a plasticizer (in this case, glycerol). They add nanocrystalline cellulose (NCC), a material made from tiny, crystallized particles of plant cellulose that, due to their small size and high surface area, can be used to add strength to materials. It also adds waterproofing properties by filling the spaces between protein molecules to block the path of water molecules.
The mixture is processed into the film-forming solution, poured into trays and allowed to dry. Then the film is peeled off and tested to check strength, flexibility and other properties.
“The problem with the NCC is that, when we add it to the film-forming solution, it prefers to bond with other NCC molecules,” Dissanayake noted. “Then they start to aggregate in the film. It’s not a good thing.”
The solution was to modify the NCC by reducing the number of hydroxyl (OH) groups, which have a negative charge. Reducing them results in a positive charge for the particles, so they start to interact with protein molecules.
The other challenge was creating the perfect balance of strength and flexibility. Dissanayake noted that bolstering one property seemed to degrade the other.
“It’s kind of challenging. We need to find that balance in all the properties.”
Potential
In the end, Dissanayake said the results are promising. Samples made during her master’s studies managed to reach that balance.
“I still have some films that I made two years ago, and they’re still really good in terms of flexibility,” she said.
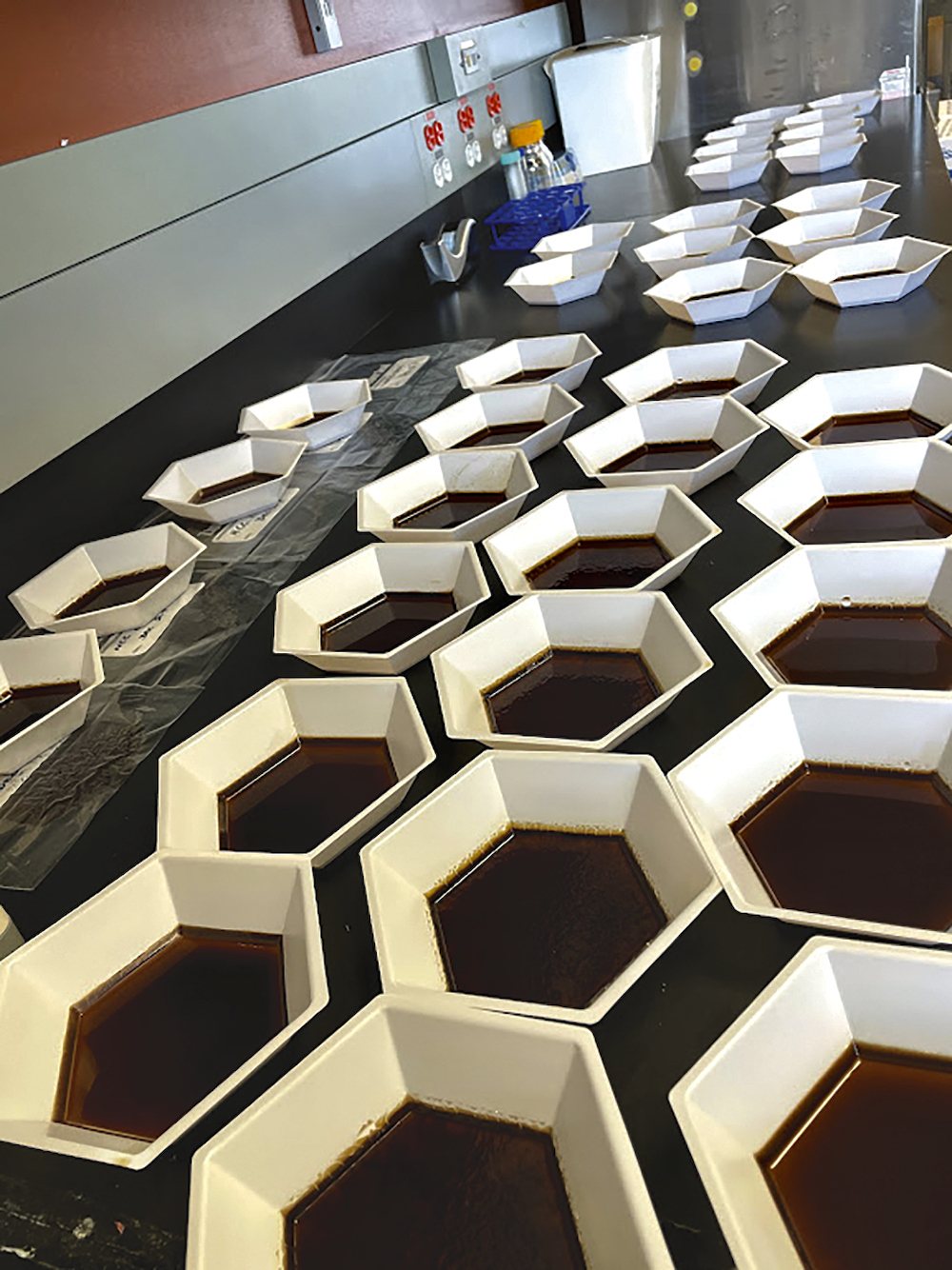
Her thesis was named the university’s 2023 Distinguished Master’s Thesis Prize winner in the applied sciences category. Dissanayake is now working on her doctorate.
Meanwhile, the food packaging research continues under the supervision of Nandika Bandara and project collaborators Claudia Narvaes and Tizazu Mekonnen from the University of Waterloo.
There is still much work to do before the films are ready for commercialization. A major step is determining how to ensure the canola protein doesn’t contaminate the food it is packaging. The protein is suitable for animal feed but not human consumption.
After that is worked out, the next step is scaling up the lab-based method to incorporate industrial film-processing technologies such as extrusion and compression moulding.
“If the technology is translated at a pilot scale, the next step is a commercial trial in collaboration with industry partners,” said Dissanayake.
To reach that point, extensive research, technology modifications and adjustments are required.
Dissanayake has poured a lot of effort into the project and thinks it’s important enough to move toward commercialization.
“It’s a good packaging material. These are good properties and it has huge potential,” she said. “And using highly available byproducts for food packaging materials makes it a more sustainable solution. That’s why we think this is important.”
– This article was originally published at the Manitoba Co-operator.