As anyone who’s seen the footage can tell you, the ‘bomb cyclones’ which hit the flooded U.S. Midwest this spring showed the force of Mother Nature at its most devastating.
The combination of heavy winds and water not only knocked grain bins over — it crushed them like aluminum cans, sending them floating down makeshift rivers with grain spilling behind in their wake.
Now that we have your attention, it’s fair to say that no amount of anchoring would ever protect a grain bin against this sort of extreme weather — such as the very high, sometimes hurricane-force, winds or the major flooding suffered by Calgary and High River in the past decade.
Read Also
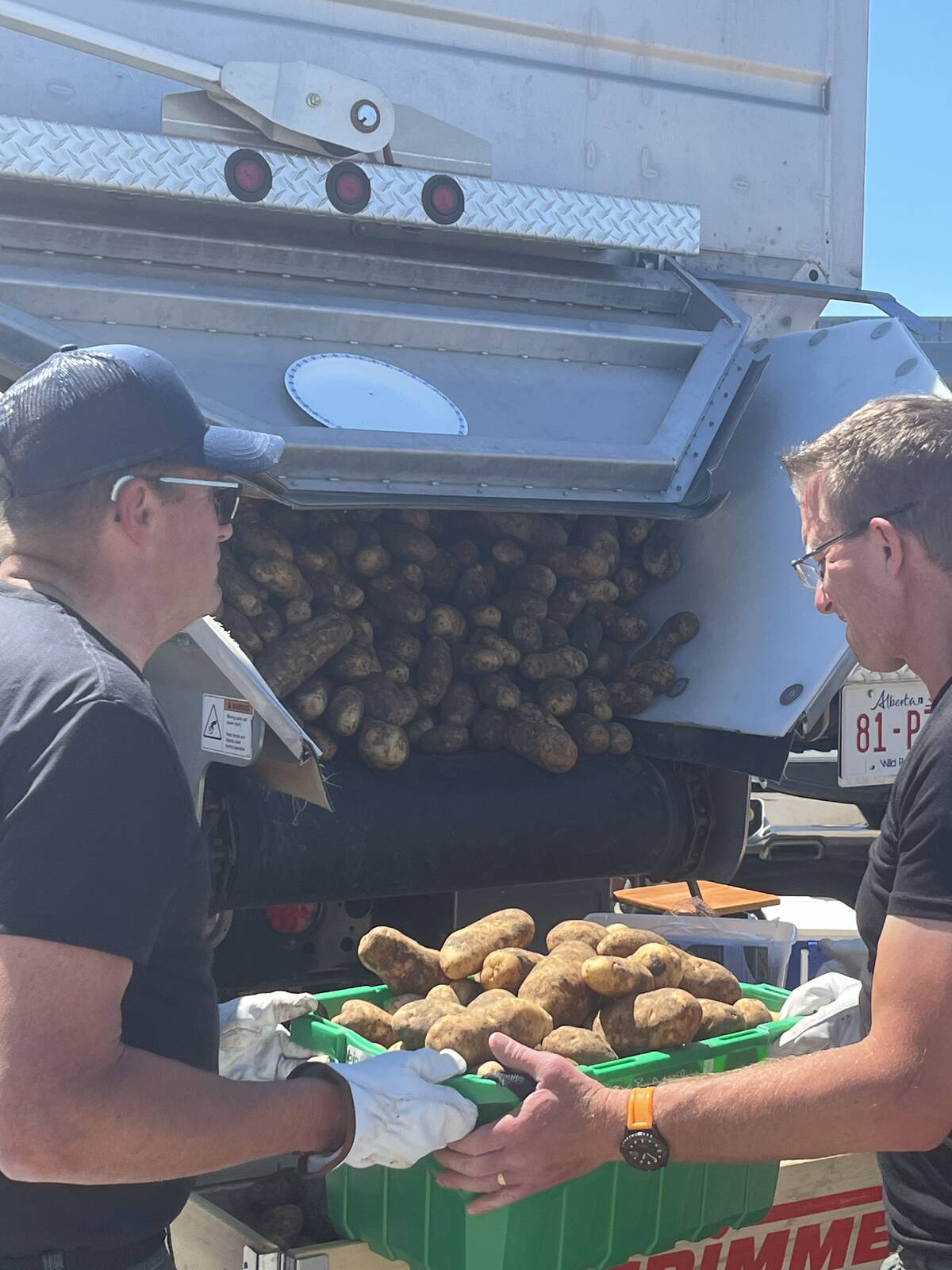
Farming Smarter receives financial boost from Alberta government for potato research
Farming Smarter near Lethbridge got a boost to its research equipment, thanks to the Alberta government’s increase in funding for research associations.
The best producers can do is hedge their bets, and most grain bin experts would agree the best bet against bin collapse is a strong base bolstered by anchoring.
According to Ryan Steinley with Flaman Agricultural Sales in Lethbridge, there have already been quite a few bin blow-overs in his area this year and the problem — at least anecdotally — is getting worse.
Most farmers understand the importance of anchoring, but with so much already on their plates it can easily become a victim of “I’ll get around to it”-itis, said Steinley.
“I think they mean to get to it but they’re in a rush,” he said.
But procrastination can be costly.
The largest flat-bottom Steinley has ever seen blow over was a 20,000-bushel bin, while the largest hopper he’s ever seen collapse was a 10,000-bushel unit that succumbed to 110-mile-per-hour wind. Both were empty.
“I wouldn’t want to be out in that kind of wind if they were full,” he said.
Base considerations
Strong anchoring begins with the base or foundation of your bin, which can be concrete, ground pads, packed gravel or skids on top of packed gravel. Concrete is by far the most secure, but in some plough winds and hurricanes, even that may not be enough. Experts generally recommend drilling anchor bolts into the concrete pad with a hammer gun in order to achieve extra integrity.
So why not just bolt a bin onto a concrete pad every time you buy a new one?
It’s not quite that simple, said Steinley. Concrete makes a bin structure more or less permanent and that may not be desirable in every situation. As well, sometimes a new bin is only needed temporarily — to handle overflow, for example, — and may be sold later on. Skid, gravel and ground foundations offer more flexibility in terms of moving bins around.
But just because a bin is not bolted onto a concrete base does not mean it can’t be secure.
In the case of gravel pads, Steinley recommends removing the dirt right down to the subsoil, filling the hole with a three-quarter-inch road crush gravel with sand and “packing the heck out of it.”
Poorly packed gravel can cause bins to come right out of the ground following a frost, said Steinley.
“When the frost comes out of the ground and you do not have an adequately packed pad the frost can actually tip bins over,” he said. “The first sign is they start to lean because they are not sitting sturdy. I’ve seen it happen a few times.”
Ground foundations are another option for producers seeking temporary bin placement. The key, say experts, is that they be installed on solid, compacted ground and secured by screw-in earth anchors.
Earth anchors
Earth anchors are ideal for hopper bins placed on less permanent foundations such as skid, gravel or ground pads. They consist of a series of anchor screws twisted into the ground using a post logger. They are equipped with auger flighting (also called a ‘helix’) which help hold them in place.
Once anchors are placed, a cable is run from the bin over the cross-member of each leg, said Steinley.
“Usually there’s an eye hook or a hole in the anchor where you can run another cable around. Most guys will use a turnbuckle or something so when the bin settles on the gravel pad you can tighten that cable back up.”
Anchor screws can be just about any size, but use the longest screws the soil can support, said Steinley.
“The bigger the flighting and the farther into the earth it can go depending on your soil type, the better.”
The number of anchors used matters. Ideally, there should be an anchor screw cabled to every leg of the bin, said Steinley, although every second leg may suffice for bins located behind buildings or otherwise sheltered from the wind.
“If you do not have sufficient anchors or not enough of them they can still blow over,” he said.
Dealerships may be able to help with the technical specs required to keep a bin in place in the event of extreme wind.
“There are specific earth anchors that a customer should look at to hold the load of that bin depending on the height and weight of the product inside of it.”
Finally, don’t underestimate the sidewall damage high winds can also cause, said Steinley.
Placing bins too close together creates a solid wall effect that can lead to denting.
Bins should be six to 10 feet apart.
“You don’t want them too far apart but no closer than two feet apart — a little farther would be better,” said Steinley.