NATURE’S WAY Potato producer says compost made from feedlot manure is an economical way to make crop production part of a natural cycle
The Kasko Cattle Company feedlot is proof that integrating cows and crops can protect the environment while boosting the bottom line.
The 14,000-head feedlot near Taber is surrounded by 10 quarter sections owned by Ryan Kasko, and Harold and Chris Perry. While Kasko owns and operates the feedlot, the Perry family’s expertise is in producing potatoes, sunflowers and peas on 4,600 owned and rented acres close to Chin, about 40 kilometres from the feedlot.
The Perrys have used cattle manure compost as fertilizer for the past decade and Harold Perry says it’s been highly beneficial. Productivity had been dropping on land under cultivation in a four-year potato crop rotation, but rebounded when compost was applied, he said. The compost not only provides organic fertilizer, but is also an excellent soil amendment, adding micronutrients and providing other biological benefits.
Read Also
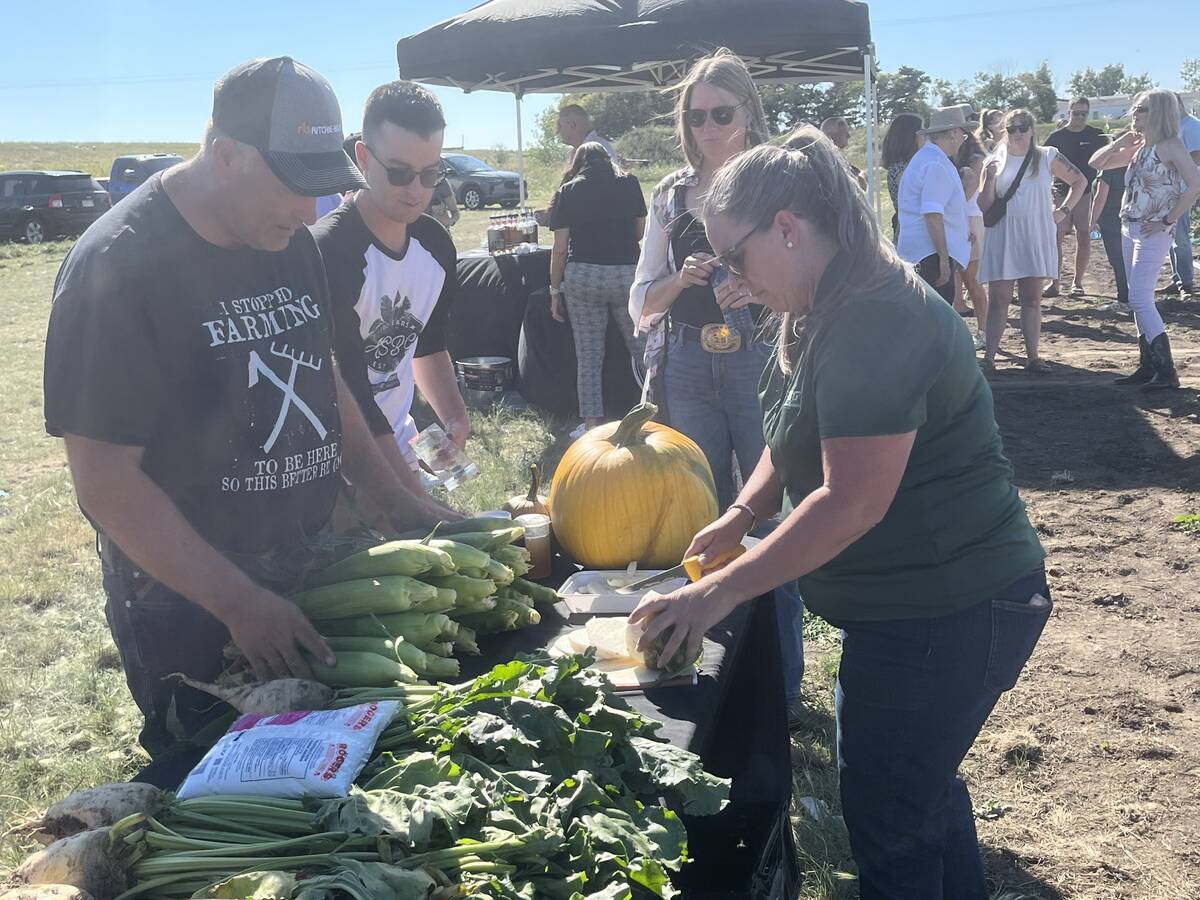
Alberta farm lives up to corn capital reputation
A Farm to Table Tour featured Molnar Farms, which grows a large variety of market fruits and vegetables including corn, with Taber being known as the Corn Capital of Canada.
“We wanted to try compost because that is the natural way that things work,” said Perry. “When the buffalo were here, they ate and manured the grass at the same time, and that’s how the natural cycle worked.”
Compost also costs less than commercial fertilizer, said Perry.
Not all the potato land is fertilized with compost — only the land they own. Since potatoes must be grown on a four-year rotation, the Perrys participate in a land exchange program with other local farmers. However, since they have no control over other people’s land, raw manure from feedlots, including some from Kasko Cattle Company, is applied on land owned by other farmers where the Perrys grow potatoes as part of the exchange program.
Until last year, the Perrys purchased compost from a commercial supplier, but Perry said making their own gives them better control over compost quality. They invested in land surrounding Kasko’s feedlot to both grow their specialty crops and acquire a raw manure source.
In addition to the agronomic value of compost, there are also financial advantages to transporting compost versus raw manure.
“Good compost has about 60 per cent of the weight of raw manure,” said Perry. “So if you get too far away from the feedlot, then the trucking just kills you.”
The Perrys pay Kasko for manure, and he hires a contractor to deliver it to a location with good drainage control located next to the feedlot. The custom manure hauler creates the windrows needed to produce compost. The feedlot delivered 9,000 tonnes of manure to the site last year and Kasko estimates the feedlot generates about 15,000 tonnes of manure annually. The remaining 6,000 tonnes of raw manure were applied in the vicinity of the feedlot.
Perry manufactured about 7,500 tonnes of compost last year, with the process taking from July to mid-October. It was then applied, worked in, and then potato hills were created for next year’s planting. At the beginning, the windrow turning was done every four or five days because of the strong biological activity underway. Ideally, the conversion process should take 10 weeks, but Perry said he prefers to wait 16 to 20 weeks.
As part of the Perrys’ adventure into composting, they hired an agriculture consultant from Sunrise Ag to soil sample and develop topography maps to help determine how much compost should be applied — a process that resulted in six application zones.
The Perrys are also planning to build an aanaerobic digester on their farm to process cattle manure, rotting potatoes, and possibly green bin waste from nearby Coaldale to produce methane gas. The gas will be used to power an engine to generate 640 kilowatts of electricity. Construction is slated to begin this year.