For “safety geek” Dan Trottier, Bill 6 was the shot in the arm that the agriculture industry needed to start the conversation about farm safety.
“Bill 6 raised awareness about safety, and now that we’ve got some awareness, we have the opportunity for extension on how to do safety on the farm,” said Trottier, owner of Tatonga Consulting, a safety services company.
“It’s raising the profile of safety in a quick manner, and it’s helping us take action.”
The Enhanced Protection for Farm and Ranch Workers Act came into effect on Jan. 1, with consultations for the act’s regulations set to start in March. But in all the furor about how the act was rolled out, the value of farm safety took a back seat to anger and frustration.
Read Also
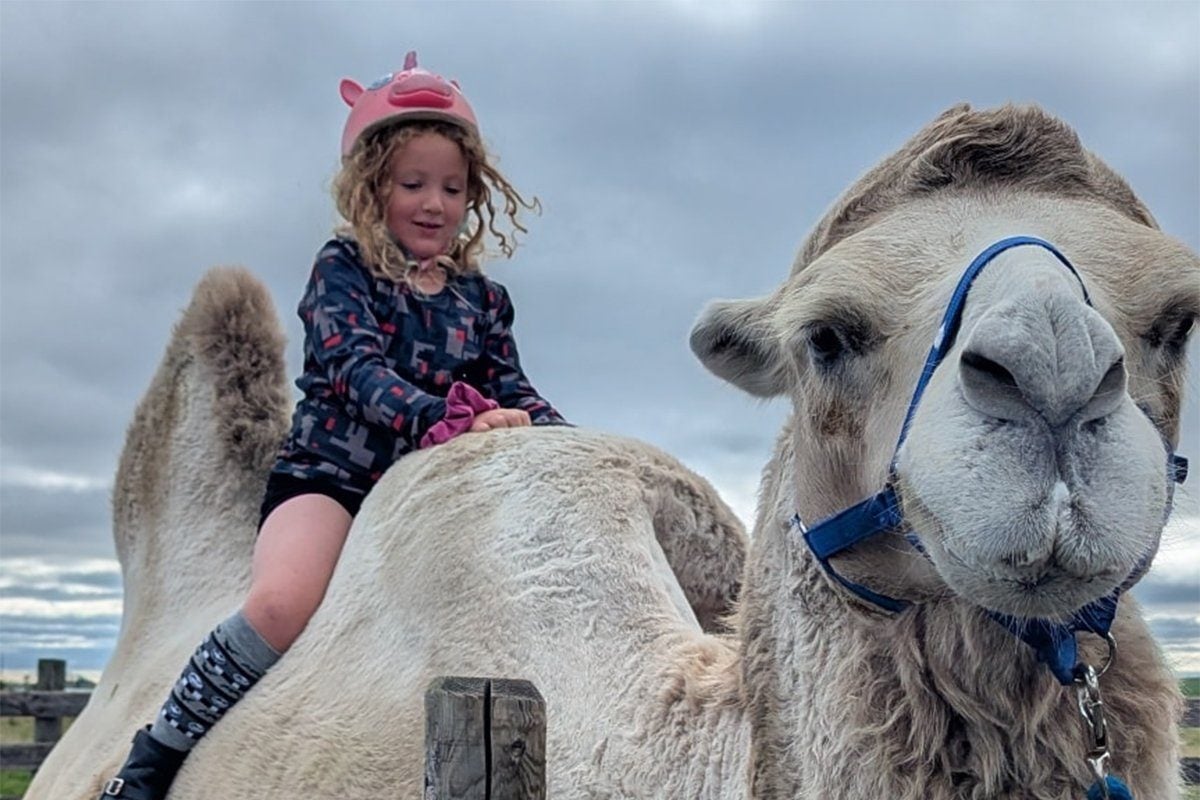
Volunteers help exotic animal farm rebuild
Exotic animal farm loses beloved camel and pony to huge hail storm that gripped the Brooks, Alta. area as a community member starts a fundraiser to help the family recover from the financial and emotional damage.
“I’m sitting here as a safety geek and wondering what the problem is. There’s so many advantages for having a safety program that contributes to the bottom-line value of your operation. What’s the hold-up?” Trottier said at a FarmSafe workshop last week.
“We all want to work safely. We all want to protect our workers.”
Every year, an average of 18 people are killed in farm operations in Alberta, said Trottier.
“Agriculture maintains the second to third spot nationally for deaths, compared to any other industry,” he said, adding injuries are harder to track in Alberta because of the lack of Workers’ Compensation Board coverage.
“In 2014, we lost 25 people in agriculture in Alberta, and two of those were between the ages of zero and 18 years old.”
In addition to the tragic loss of life as well as serious injuries, there is the financial cost of lost output, repairs, and other costs.
“The Canadian Agricultural Injury Reporting data suggests that if you have a workplace fatality, the rule of thumb is that it’s going to cost your business over a quarter-million dollars,” said Trottier.
“If you have someone who has a permanent disability, it costs $143,000. Somebody who’s hospitalized costs $10,000. A minor injury requiring first aid costs $700.
“For a hospitalization that costs $10,000, how many sales do you have to generate to offset that cost to your business?”
Farmers try to be safe, and generally are, but usually more can be done to reduce the risk, he said.
“Everybody wants to be safe. We just don’t take the time to talk about it or formalize that process.”
Hazard assessment
Producers can begin that process by “making that commitment to a safety program,” he said.
“The FarmSafe plan is a great resource because it walks through the steps that need to be done,” said Trottier.
(The guide can be found at www.agriculture.alberta.ca — search for ‘farmsafe guide’.)
But producers should “start small and keep it simple,” with a formal assessment of the hazards on the farm.
“Your hazard assessment and control program is the foundation of your safety program. We want to understand what the hazards are and eliminate them in the operation,” he said, adding that hazards can be chemical, biological, physical, and even ergonomic.
“If you’ve got your farm safety plan set up properly, you’re going to cover 80 per cent of the issues you’ve got on your farm with your formal hazard assessment.
“Start with those issues on your farm that represent 80 per cent of the risk for your operation, and the rest will come later.
“We’re not here to build a 100 per cent program. We’re here to build a start.”
The first step is creating an inventory of jobs to pinpoint the hazards of what you do on a day-to-day basis.
“I can remember dearly the days on the farm being the electrician, the plumber, the farmer, the welder, the vet, the carpenter — we do it all,” said Trottier.
“Look at each job and list the associated tasks with it. Then you can start identifying hazards for those job tasks.”
Then focus on the jobs with the biggest risks, added Trottier.
“You know what’s the most dangerous thing you do on your operation.”
Risk is often based on perception, “but we can actually put numbers to it,” he said.
“We can analyze each job step by looking at severity, which is consequence of exposure, the probability that the hazard is going to cause something to happen, and the frequency of how often we’re exposed to that hazard over time,” he said.
From there, producers can determine the value of total risk, by assigning low-risk tasks a value of 1, medium-risk ones a value of 2, and high-risk tasks a value of 3.
“We multiply severity by probability by frequency and generate a number that represents a value of risk for that job step.”
Once producers have identified the risks on their farm, they can begin to manage them through control measures and training, said Trottier.
Taking those first steps — however small — will help producers show that they’ve done their due diligence should Occupational Health and Safety officers come knocking at the door.
But having a farm safety program “shouldn’t be driven by legislation,” said Trottier.
“Most of the systems I see that fail are because it’s just done to get the check mark,” he said.
“It should come from the desire for the farm to have a safe work environment for its workers and to take advantage of productivity gains.
“You need to do it for yourself first.”