Glacier FarmMedia – In the 1970s, a standard bin was 14 feet in diameter with a capacity of 1,350 bushels. High rollers might add an extra ring to stretch that another 300 bu.
There were bins 19 feet in diameter, with a 2,700 bu. capacity, but few farmers bought them because they were hard to shovel out and sweep augers weren’t widely available.
These days, the numbers are a lot bigger. The most common flat-bottom bins today are 36 and 42 feet in diameter and store 25,000 to 40,000 bu., says Derek Johnson of bin maker AGI.
Read Also
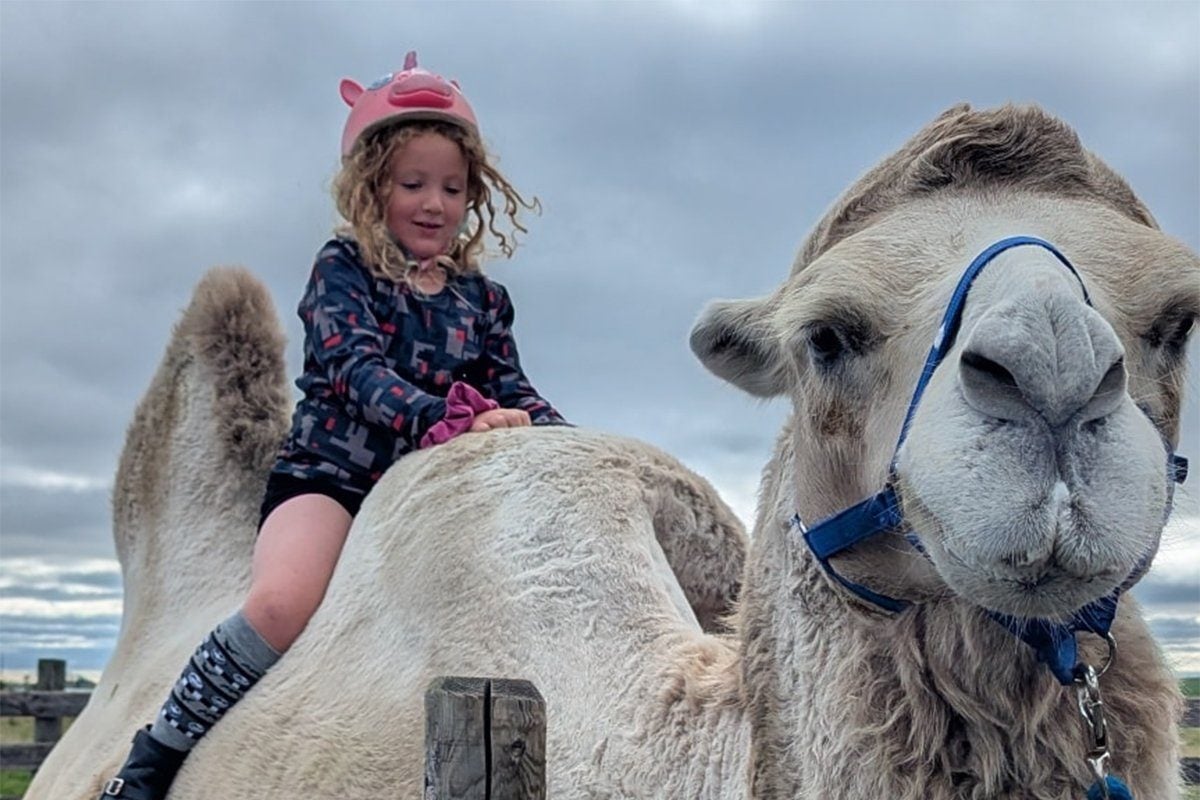
Volunteers help exotic animal farm rebuild
Exotic animal farm loses beloved camel and pony to huge hail storm that gripped the Brooks, Alta. area as a community member starts a fundraiser to help the family recover from the financial and emotional damage.
“Over the last 10 or 20 years, the size of bins has grown dramatically, just based on sheer production. We know genetics have improved, farming practices have improved and with that comes an increase in production.”
That brought a push for larger bins, more sophisticated grain-handling solutions and high-tech monitoring equipment.
“Growers are looking for a system that’s fairly easy to run and fairly easy to maintain,” Johnson says. “That comes down to the monitoring systems that they’re putting into their bin, being able to see the condition of their grain on their phone, being able to control their fans — being able to turn them on when they see there’s potentially a hot spot in the bin and condition that grain down and keep it cool.”
Putting that much cereal grain, pulse or oilseed in one place for an extended time comes with a challenge to keep that product safe and in condition.
Just the effect of that grain’s weight pressing down is significant. A 19-foot bin from the 1970s could hold roughly 162,000 pounds of wheat, assuming a bushel weight of 60 lb. The biggest bins of today hold 2.4 million lb., nearly 15 times as much.
That packs grain tightly into the bottom of the bin and increases static pressure (resistance to airflow), making temperature and moisture control more difficult. Those challenges are offset by lower cost per bushel and less hassle switching from bin to bin during harvest and grain shipping.
Grain price trends over the years makes the math better, too. Farmers can typically get the best price several months after harvest.
“That’s when those grain companies are looking for product,” Johnson says. “To capture those premiums in the marketplace, you have to have safe storage.”
While grain bags have recently grown in popularity, they’re better suited to short-term storage to ease harvest logistics. Grain can be stored in them for longer periods, but not as reliably and with considerable risk and management requirements.
One grain storage specialist says managing a bin isn’t complex, but farmers need a clear picture of what’s happening inside.
Wayne Clews of Clews Management says many farmers guess the condition of the crop in the bin and run fans as a safeguard. However, that can work counter to their best interests.
Rather than incrementally reducing the temperature of grain as the air temperature co-operates, an up-and-down tug of war ensues. A cool night cools the grain and warmer days bring the temperature back up.
“You can actually be hurting yourself,” Clews said during the Ag in Motion outdoor farm show this summer near Saskatoon. “You’re better off if you know what’s happening in the bin. That’s where it starts.”
Clews said recent advances have made it easier to monitor temperature and manage fan operation.
“I sold my first cable [to monitor bin temperature] in 1969,” he said. “Back then, you had to drive into the bin yard, maybe move a little snow, and plug into the cable. These days you can take a cup of coffee into your office in the morning, get on the computer and in a few minutes know what’s happening in your bins.”
That doesn’t necessarily mean bin monitoring is universal. It’s pretty much standard equipment on new large-capacity bins, but there are still a lot of older, smaller bins with no sensors.
In the end, it comes down to three factors, Clews said: the moisture of the grain; the temperature of the grain; and how long the farmer wants or needs to store it. That equation can change based on variables like commodity prices.
“When canola falls from $20-something to down into the teens… there’ll soon be some out there that’s over 365 days [in storage],” Clews said. “That’s a whole new challenge. What was safe for 200 days may not turn out to be all that safe for 300 days.”
That’s when close monitoring of a bin can pay off.
While a physical sensor in the bin itself is the gold standard, there are other approaches to manage grain storage that rely on data, not cables.
OPI has been a leader in grain storage technology for decades. It’s taking a new approach that provides some free hardware, offers a user-pay model for some services and a service that uses virtual weather data to alert farmers on the optimum time to run their fans, says the firm’s founder and owner, Dave Crompton.
“We’re trying to knock down some of those barriers to entry and get people into the tent and talking and thinking about grain storage differently.”
Crompton says the hardware-based approach is always going to be the gold standard but OPI aims to give producers smaller, easier steps to get there.
“We feel that’s a better approach than asking people to make this major paradigm shift from the way they’ve always done things — or even the way their parents and grandparents always did things — all at once.”
– This article was originally published at the Manitoba Co-operator.