Glacier FarmMedia – We’ve come a long way with sprayers. We’ve made them bigger, we’ve made them faster and with new visual technology and artificial intelligence, we’ve even made them smarter.
Now, research by the Prairie Agricultural Machinery Institute (PAMI) along with the College of Agriculture at the University of Saskatchewan and Agrimetrix in Saskatoon is asking, ‘Can we make them more aerodynamic?’
Spray placement is already a complex equation of wind and other weather conditions, but how does air disturbance from the sprayer itself factor in?
Read Also
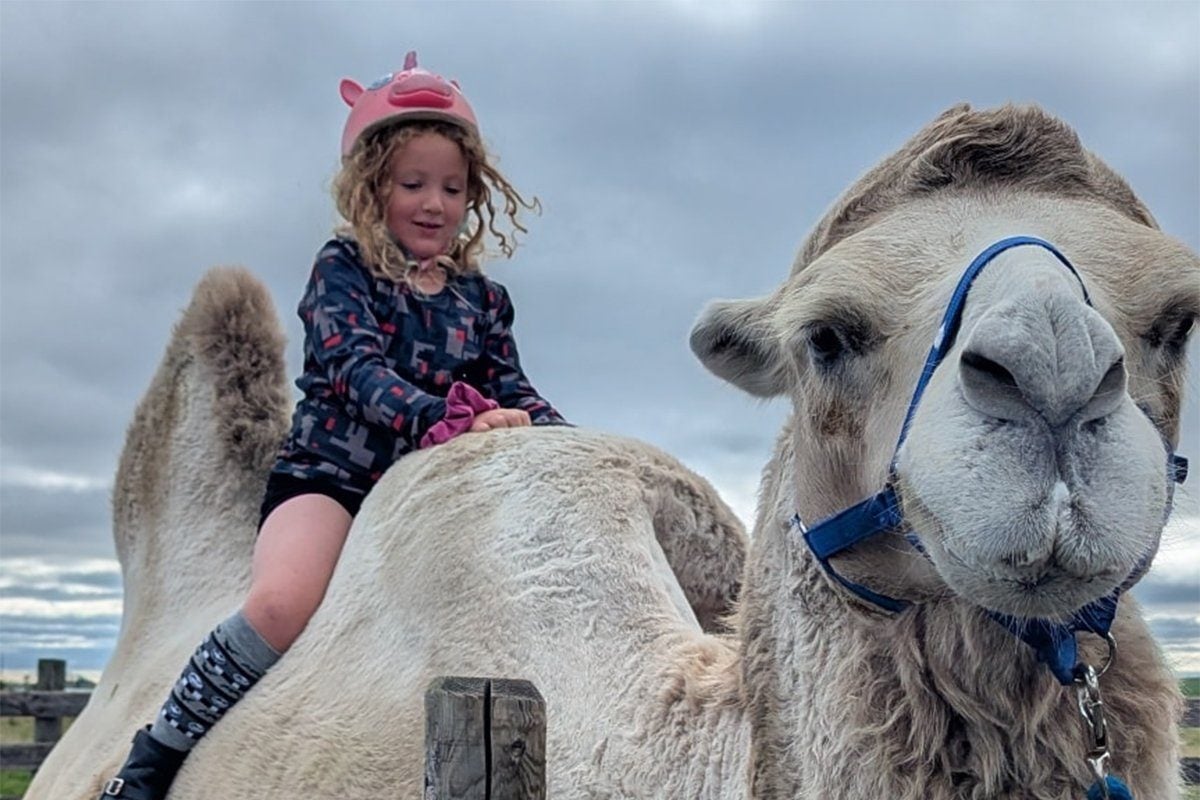
Volunteers help exotic animal farm rebuild
Exotic animal farm loses beloved camel and pony to huge hail storm that gripped the Brooks, Alta. area as a community member starts a fundraiser to help the family recover from the financial and emotional damage.
It comes down to air disturbance from the sprayer.
It’s simple to assume that a boom with nozzles pointed straight down is going to put that spray onto the crop or the soil. Under the best of conditions, this is true, but nature rarely provides the best of conditions.
“Drift is not beneficial. We want to concentrate the spray in the area that it is desired and not have it go anywhere else,” said Lorne Grieger, PAMI’s director of technical sales. “When you’re looking at the sprayer, how it’s physically put together in terms of the structure and how it’s operated, we want to understand how that impacts the potential for spray drift.”
If you’ve ever watered a garden patch by putting your thumb over the end of the hose, you have an idea of how hard it is to get an even spray exactly where you want it. You’ll have droplets of all sizes going in several different directions. Some spots will get more water than others.
A hose nozzle from the local hardware store will do a better job of even coverage and give you options ranging from a long jet of water to a fine mist. Still, it may be confounded by a sudden breeze that can misdirect the stream.
In the garden, this isn’t a serious problem. With a pesticide, it certainly can be.
You don’t want anything drifting across the road to do damage in a neighbouring field. You want to account for every drop.
Measuring disturbance
The PAMI team’s work started with a computer simulator to get a broad idea of where drops might go during application.
“We used a tool called Computational Fluid Dynamics, which is a computer simulation of air flows,” Grieger said. “Then we coupled that with the equipment to understand what the impacts or implications are with using the physical structure of a high-clearance sprayer.”
Modelling a moving sprayer is more complex than you might think. It’s a solid object moving through the air while it dispenses a liquid out the back from a long boom. As it moves, it sets up small eddies and whorls within the air. To make it even more complicated, that air is moving too. This can have all kinds of influences on where the spray goes.
“Part of the simulation process is simplifying… a very complex type of system,” Grieger said. “This allows us to break it down into something that can be modelled and can be solved.”
The computer separates the equipment into its component parts: the tractor, the tank and the boom. The software can calculate how air would move around the different shapes and how it would probably act in very specific locations.
Researchers can then tweak some of the inputs such as ground speed or wind direction and come up with a good idea of how the air will behave around the sprayer and how it will affect the spray itself.
Once satisfied with the data, it was time to test the model in the real world.
“We did simulation work looking at a self-propelled sprayer operating in the field.” Grieger said.
Grieger’s team mounted several small anemometers — sensors to measure both the direction and speed of the air at several points behind the sprayer and around the boom.
“The intent of using the anemometers was to understand how laminar or how turbulent the air would be at various locations behind the sprayer and the boom itself,” Grieger said. “We wanted to understand the direction of the air. Is it going straight or is it going to the side? Or it also may be going up.”
That last option, he noted, would certainly have the potential for extra drift.
Laminar flow is a layer of air moving from one point to another, very much like the air flowing from a furnace vent. Under ideal circumstances, it will flow straight and unimpeded along the floor. Staying with the vent analogy, when the dog walks into the warm stream, curls up and lies down, there is suddenly an uneven obstacle that the air has to move around. The dog is now a source turbulent flow. If he’s lying on his back with his legs in the air, the effect is even greater, since the strange shape can cause the air to move in strange directions.
That sleeping dog is a simpler obstruction than a sprayer moving across the field.
“The combinations of the physical components can impact what you see behind the unit itself,” Grieger said.
If there’s a slight breeze blowing, it may be a laminar flow straight over the square cab, but it starts to move in all kinds of directions as it meets the less regularly shaped tank, tires or the boom, with all its hoses and superstructure. These are the eddies that wind up slipping under the nozzles, thus influencing drift.
There were a few takeaways from the work, some of which echoed standard advice from spray experts. Grieger’s team noted lower drift potential in lower boom heights and slower ground speeds, although a caveat on that last point noted that varying conditions mean there is no perfect speed setting for spraying.
The other thing they found, however, was that the aerodynamic efficiency of the boom was affected by the width of the tractor portion of the machine. Nozzles closer to the end of the boom were less affected by turbulence caused by the machine in the middle.
Impact
What Grieger’s work was really developing was research methods for analyzing the engineering of future farm equipment. The ideas generated by this kind of research could contribute to the development of better simulation software and better design and operation of equipment like sprayers.
“This is the first step in terms of overall understanding. What does it look like in the field when you’re using a high-clearance sprayer? What does it do to your spray drift potential?” Grieger said. “And then, once you have the data, you can use that as a benchmark for making any adjustments or changes to the implement.”
– This article was originally published at the Manitoba Co-operator.