Cattle producers could save themselves a fair bit of time and money — if they’re willing to make the shift from standard low-frequency RFID tags to a new ultra-high-frequency alternative.
“The typical button tag has been around for a long time and works very well, but it’s in a low-frequency spectrum and the read range is therefore very, very short,” said Glen Kathler, applied research chair of the Radio Frequency Identification Application Development Lab at SAIT Polytechnic.
“With this ultra-high radio frequency technology, now you have a tag that you can read from up to 20 feet away, and you can also read more than one tag at a time.”
Read Also
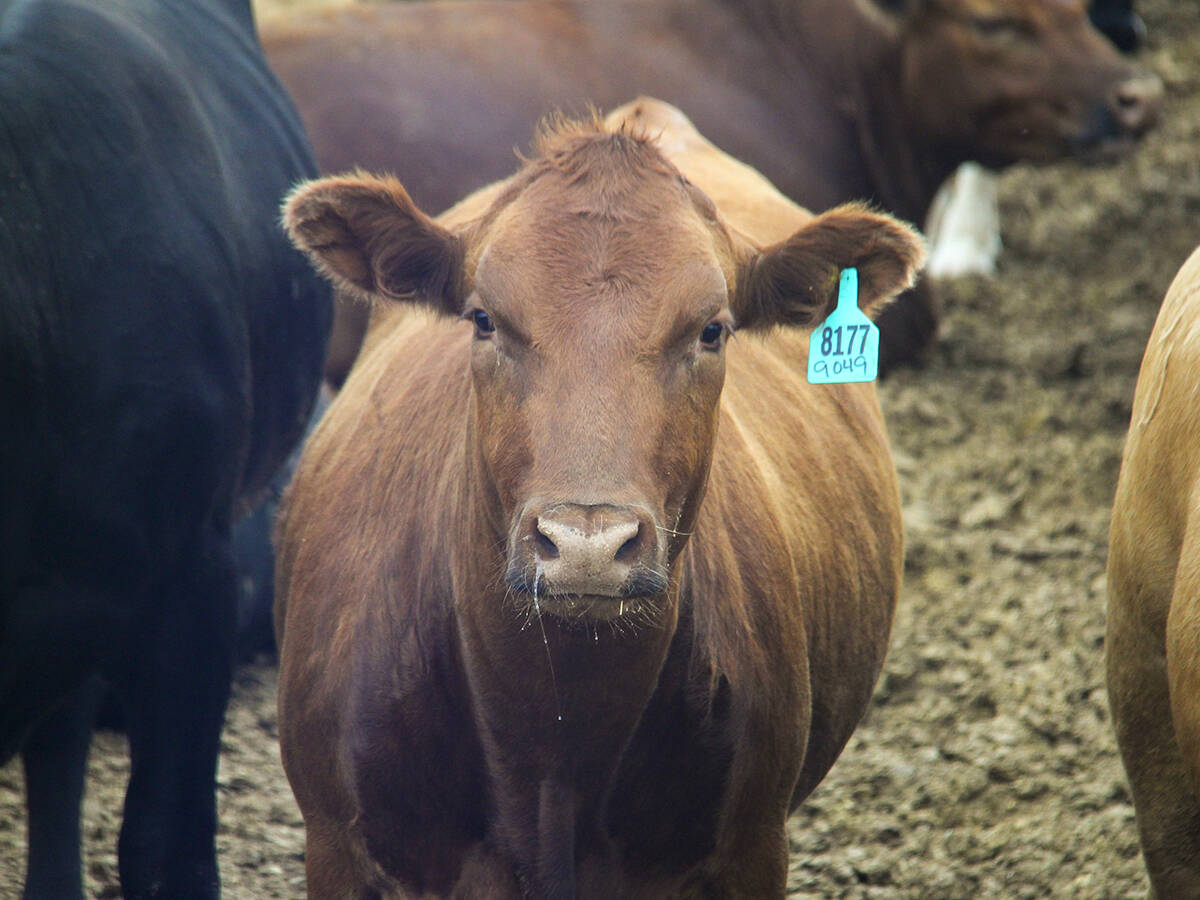
Countdown begins for traceability
Canadian cattle producers are awaiting new federal traceability regulations following a two-year consultation process.
The Calgary school was approached in 2011 by Livestock Identification Services to see if there was technology to improve cattle traceability. LIS and the Canadian Food Inspection Agency were interested in things such as real-time tracking of cattle during transport and enhanced disease traceability when animals commingle.
“We looked at the whole supply chain, right from the producer all the way to the packing plant — with stops at the auction markets, the feedlots, and the transport companies — to see where some of the biggest gaps are,” said Kathler.
Ultra-high-frequency RFID tracking — widely used in areas as diverse as oil and gas, manufacturing, and prisons — seemed like the way to go, not just for agencies like LIS but also producers. Kathler uses the example of a producer loading cattle or moving them to a new pasture.
“He could literally take something out of his saddlebag, stick it into a fence post for 20 minutes while he moved animals, and it would just read all of the tags of the animals going through the gate,” said Kathler.
“It’s very automated, and it simply creates a higher level of accuracy as opposed to trying to read something visually, as well as having to be so close to an animal that you can read a tag with a low-frequency wand reader.”
The technology would also be highly useful at auction marts for tracking animals from pre-sale pens through to loading. But it’s feedlots that stand to gain the most, he said.
“Just the ability to sort animals, to move animals, and to read tags without adding any additional stress by having them go through the squeeze chute was a big attraction for that particular market,” said Kathler, adding cattle are conservatively estimated to lose one per cent of body weight from stress each time they go through a squeeze chute.
“We showed that if you could eliminate even one of the trips through the squeeze chute to get its tag read, there’s a significant cost savings because there simply would be no stress on the animal. They don’t know they’re being read. They’re not being squeezed. They’re just being moved from one pen to another.”
Other benefits
And because the system can read multiple tags at once, there’s a big time savings, too.
“We can have animals go through a wide alley as they’re sorting from pen to pen, and we can read all the tags, even if they’re going one at a time or we’re bunching them 20 or 30 or 200 or 300 at a time through the alley.”
Ultra-high-frequency systems are also one-tenth the cost of their low-frequency cousins, and have impressive accuracy.
“We did roughly 4,000 squeeze chute tag reads, and we only ever read the tag we were trying to read,” said Kathler. “People were wondering if they were going to read all the animals in the tub way behind the animal in the squeeze chute, and we showed that you only read the animal in the squeeze chute.”
His team also installed readers in two cattle liners and hauled a few loads to Cargill’s High River plant.
“We captured a real-time cloud-based manifest of the 48 animals and the exact inventory list of those animals,” said Kathler. “The reader on the liner automatically uploaded its loading and unloading manifest into the cloud, and we were able to compare those two manifests to show that there is the ability with this technology to create this automated shipping manifest that would allow for better traceability.”
More testing is planned for this spring at Olds College, which will allow researchers to study a single herd for 35 to 40 weeks.
But while everything has been highly promising so far, widespread adoption of the technology is a ways off.
“It is probably in the three- to five-year window before it would even be approved for use in traceability,” said Kathler, adding that he expects the feedlot sector will be keenest to adopt the technology.
There may be a period when both technologies exist side by side, and one tag manufacturer is making a dual-purpose tag, with both low-frequency and high-frequency components.
“In essence, the tag could be approved for use by the Canadian Cattle Identification Agency for its low-frequency capabilities, but it now also has this ultra-high-frequency portion to it as well.”
Kathler’s team has also developed a smartphone reader that can read both types of tags.
“We’re trying to look at as many ways as possible when it comes time to transition to make it as easy as possible for any portion of the industry to consider adopting it.”
The four-year, $1-million research project was funded by the Alberta Livestock and Meat Agency.