Making plastic out of cattle parts sounds like science fiction but it s become a reality, thanks to University of Alberta researchers.
The process developed by David Bressler and his team transforms specified risk material (SRM) from cattle rendering into plastic, thereby transforming a waste product and keeping it out of landfills. They ve developed a process that breaks down big pieces of protein and reforms them. Prions the suspected cause of BSE are destroyed in the process, making the material safe.
Read Also
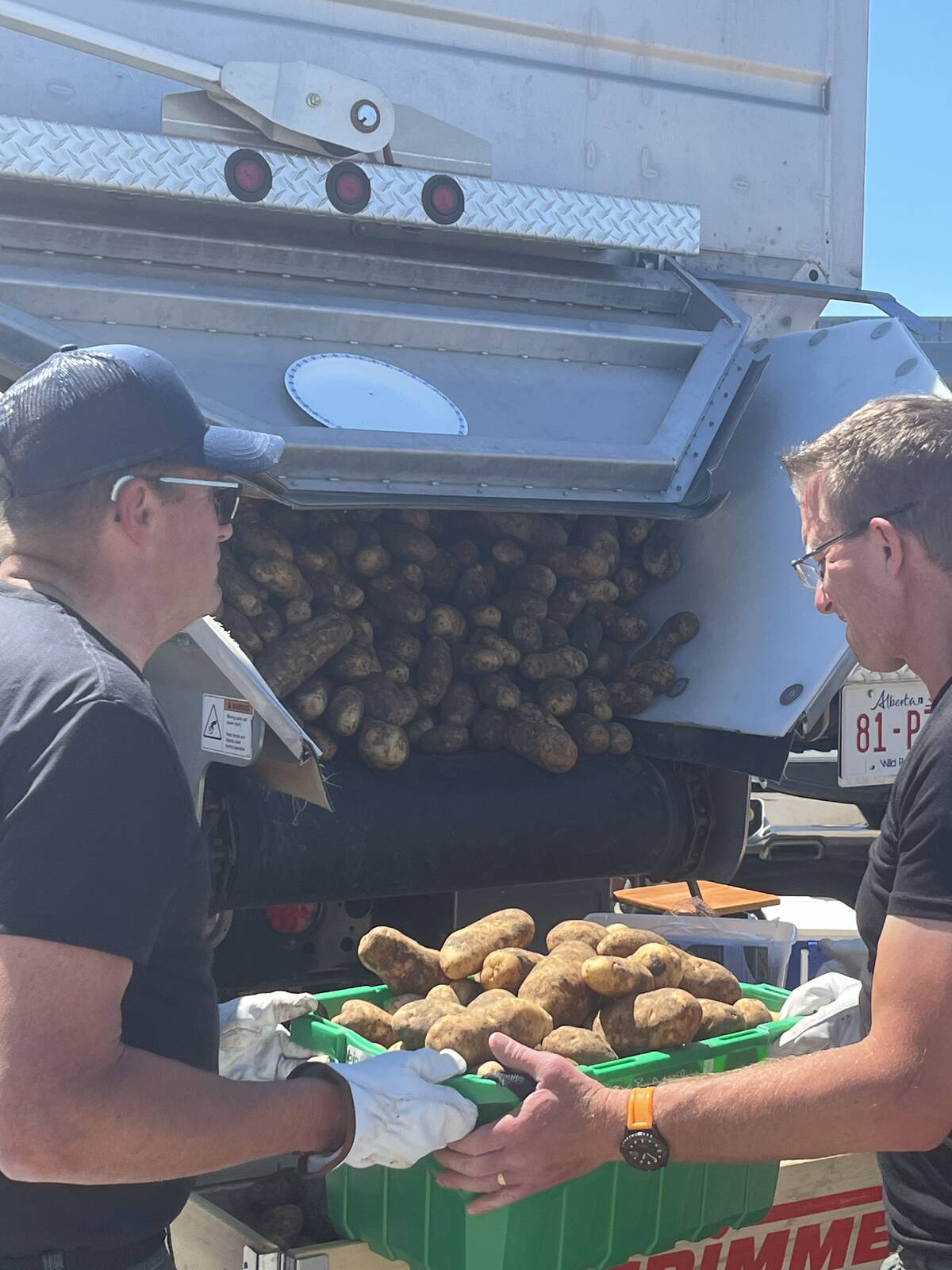
Farming Smarter receives financial boost from Alberta government for potato research
Farming Smarter near Lethbridge got a boost to its research equipment, thanks to the Alberta government’s increase in funding for research associations.
The researchers, working in the only lab in Canada certified to conduct research on SRM materials (which includes bovine spinal columns and brains), used thermal and caustic hydrolysis to break down the components.
It goes from what looks like a powder with bones and hairs in it, to what looks like a black molasses with fragments in it, said Bressler, an associate professor at the University of Alberta s Agriculture, Life and Environmental Science faculty.
The research team developed a technique to extract the protein from the mixture. All proteins have different cross-links in nature. Hydrolysis shreds the cross-links between the prions, rendering them non-functional. The researchers then found a way to rebuild these proteins into a plastic, which can be pliable or stiff, depending on how the cross-links are combined.
What the chemistry was really about was changing the type of cross-links and the amount of cross-links that we are using, said Bressler. Eventually, it is one big molecule at the end, way bigger than the original protein.
The hope is this very unusual recipe could save money for processors and renderers, which could, in turn, benefit producers.
What is exciting is that our feedstock is cheaper than hydrocarbon, said Bressler. People are paying to get rid of it, and it s an environmental bad news story.
The research team has consulted experts in the automotive sector and is now changing its plastic blends to meet automotive requirements.
The automotive sector has some of the best people in plastics, said Bressler. They have a lot of expertise and they re really good at it.
Over the next year, the research team will be working with an international auto-parts maker, The Woodbridge Group, to optimize recipes for different applications. Testing of the new plastic material will likely take at least two years, and possibly much longer.
We re not sure where it will go, but we ve targeted long term high value and will just see where it goes, said Bressler.
However the research has already garnered international attention, and Bressler has done interviews with media from the United Kingdom, the United States and Australia.
The project was funded by the Alber ta Lives tock and Meat Agency, the Alberta Prion Research Institute, and PrioNet Canada.
———
Thehopeisthis very unusualrecipe couldsavemoney forprocessorsand renderers,which could,inturn,benefit producers.